刚做好的生产计划,怎么一执行就“货不对板”了呢?
在制造业摸爬滚打的朋友肯定懂这种痛:熬夜敲定的生产计划,落地时却成了“卖家秀与买家秀”——说好准时交货,结果生产线三天两头掉链子;计划里的高品质产品,实际瑕疵频出;物料消耗更是算不准,不是缺料停工就是积压浪费。
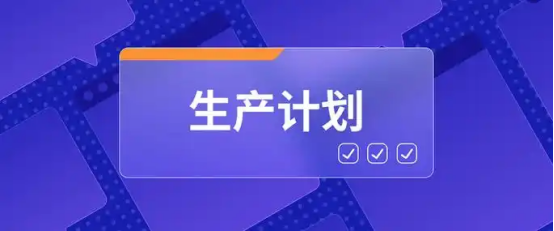
执行“翻车”现场有哪些名场面?
最常见的就是进度失控。有些企业为了赶订单,工人三班倒,机器连轴转,最后还是延期交付,急得客户天天催单;还有些企业生产像开盲盒,过度生产导致库存堆成小山,不仅占用大量资金,仓储成本也跟着水涨船高。
质量更是容易“掉链子”,实际生产的产品和计划标准相差甚远,好不容易生产出来,却因为质量不达标要返工重做,时间、人力、物料全浪费。
物料管理也是“重灾区”,缺料时生产线只能干瞪眼等米下锅,多买的料又成了闲置资源,每一项都在偷偷啃食企业利润。
这些问题看似是小毛病,实则是大隐患。交付不及时会直接丢客户信任,严重的可能直接被客户拉黑;质量差不仅砸口碑,还可能面临赔偿风险;成本飙升更是直接影响利润,挤压企业生存空间。更要命的是,一个环节出问题,整个生产节奏都被打乱,后续排产、采购、销售全跟着乱套,恶性循环一旦形成,企业就像陷入泥潭,越挣扎越难脱身。
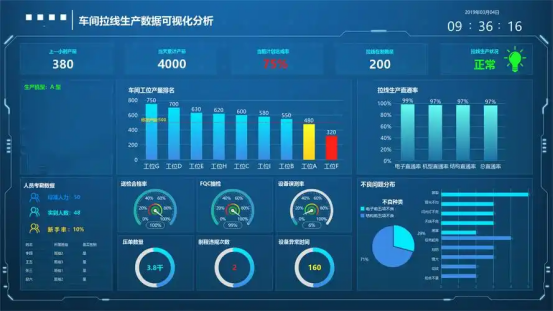
计划“变味”的三大元凶
计划制定太“理想化”:不少企业做计划就像拍脑袋决策,全靠“我觉得”“应该行”。设备明明用了好些年,故障率越来越高,却还按新设备的产能来算,结果实际生产中三天两头出故障;原材料价格波动大、供应商供货不稳定,却完全没考虑这些风险,等到要用料时才发现要么涨价要么断供;市场需求天天变,计划却定得死死的,遇到突发订单或者需求骤降,根本没法灵活调整,只能眼睁睁看着机会溜走或者产品滞销。
很多企业做计划时,各部门就像在“自说自话”。销售部门只管接订单,不考虑生产能不能按时完成;生产部门闷头排产,不管物料供应跟不跟得上;采购部门按照老经验备货,不了解生产计划的变动。这样拼凑出来的计划,从一开始就漏洞百出,执行时不出问题才是怪事。
执行管理像“放羊”:设备突然坏了,生产部门忙着抢修,却没及时把维修需求传给采购部门,结果等配件到货时,生产线已经停工好几天;质量出了问题,质检部门发现了,却没有及时反馈到生产端,导致后续生产的产品还是不合格。信息不流通、沟通不及时,再完美的计划也会在执行中走样。
执行过程缺乏监督,就像放羊一样,全靠员工自觉。员工操作不规范没人管,不按标准流程生产也没人纠正,质量自然难以保证。再加上新员工培训不到位,对生产计划理解不透彻,操作技能也不熟练,执行起来自然是状况百出。有些企业甚至连基本的执行标准和流程都不明确,员工全凭经验干活,这样的生产管理,怎么可能不出问题?
外部环境太“善变”:供应链稍微有点风吹草动,生产就跟着遭殃。原材料产地突发自然灾害,交通中断,物料运不过来;供应商自身出了问题,产能下降或者质量不达标,企业却毫无准备;物流环节出状况,运输延迟,都会导致生产线停工待料。更要命的是,现在的市场需求变化比翻书还快,消费者喜好说变就变,竞争对手突然推出爆款产品,直播带货一夜带火某个品类,如果企业不能及时感知并调整生产计划,就只能眼睁睁看着订单溜走,库存积压。
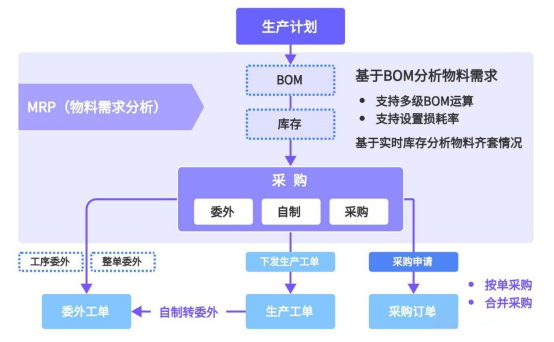
手把手教你如何做到有效的生产计划
让计划更“接地气”:别再用老数据“糊弄”新计划!企业要建立完善的数据收集和更新机制,定期统计设备运行时间、故障率、产能数据,实时跟踪物料消耗情况,把这些数据当作制定计划的“地基”,地基打牢了,计划才能靠谱。
可以把长期计划拆分成一个个小段,比如每周或者每月根据实际生产进度、市场变化情况进行动态调整,让计划始终贴合实际。做计划时一定要打破部门壁垒,拉上生产、采购、销售、仓储等部门一起开会讨论。销售部门分享市场需求预测和客户订单情况;生产部门根据产能和设备状况提出排产建议;采购部门反馈物料供应风险和价格走势;仓储部门说明库存情况。把信息都摆到桌面上,再综合考虑各方面因素,这样制定出来的计划才更科学、更合理。
执行管理要“盯紧”:搭建一个高效的内部信息共享平台太有必要了!通过平台,生产进度、物料需求、设备状态等信息可以实时同步,哪个环节出了问题,相关人员都能第一时间知道,及时沟通解决。比如设备故障了,生产人员在平台上一键提交维修申请,采购部门马上就能看到配件需求,安排采购;质量检测结果也能及时上传,生产部门根据反馈调整生产工艺,避免问题扩大。设置关键监控点,比如每天检查生产进度是否达标、抽检产品质量、核对物料使用情况,一旦发现偏差,马上启动反馈流程,责任到人,限期整改。
对于员工,要制定分层分类的培训计划,新员工入职时,系统学习生产流程、操作规范和生产计划要求;老员工定期参加技能提升培训和新设备、新工艺学习,确保整个团队都能准确执行计划。
应对变化要“留一手”:和核心供应商建立深度合作关系,绝对是明智之举。除了签订长期协议,明确供货质量、价格、交期等条款,还可以一起制定应急预案,比如遇到突发情况时的紧急供货方案,甚至联合备货,共享库存信息。定期和供应商开沟通会,及时了解对方的生产状况和潜在风险,提前做好应对准备。
市场变化莫测,企业必须要建立敏锐的市场感知能力。安排专人负责市场调研,通过线上数据分析、线下走访客户、参加行业展会等方式,及时掌握消费者需求变化、竞争对手动态、行业趋势走向。利用大数据分析工具,对市场数据进行深度挖掘和预测,为生产计划调整提供有力支撑。一旦发现市场有变化苗头,迅速评估对生产的影响,灵活调整生产计划,优先生产畅销产品,减少滞销产品产能。
根治问题的长效大招:建立一套完善的风险预警机制,做到未雨绸缪,在问题来临的时候才不会自乱阵脚。通过实时监测生产、供应链、市场等各个维度的数据,设置合理的风险指标和阈值,一旦某项指标出现异常,系统自动发出警报。比如原材料库存低于安全值、设备故障率突然升高、市场需求波动超过预期等情况,企业可以根据预警信息,提前制定应对策略,把风险扼杀在萌芽状态。
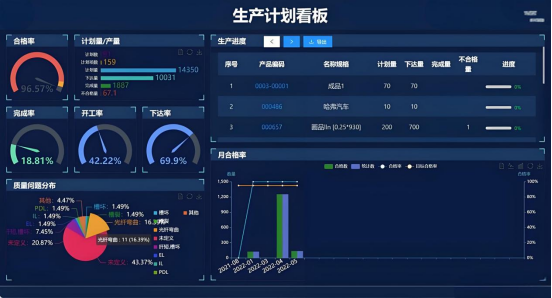
如果企业条件允许,引入一套先进的 ERP(企业资源计划)或 MES(制造执行系统),绝对能让生产管理上一个大台阶。这些系统可以实现从计划制定、资源调配、生产执行到质量检测、成本核算的全流程数字化管理,数据自动采集、实时更新,计划执行情况一目了然。通过数据分析提供决策支持,提升管理效率和精准度,生产计划从纸上到落地,确实是个技术活,但只要咱们找准问题、对症下药,从计划源头到执行细节都抓好,再配上长效预防机制,告别“货不对板”、实现高效生产真的不是梦!
下次再做计划,心里是不是更有谱了?要是还有啥疑问,欢迎随时联系!
评论