提升质量透明度,动力电池企业的数据驱动生产实践 | 数据要素 × 工业制造
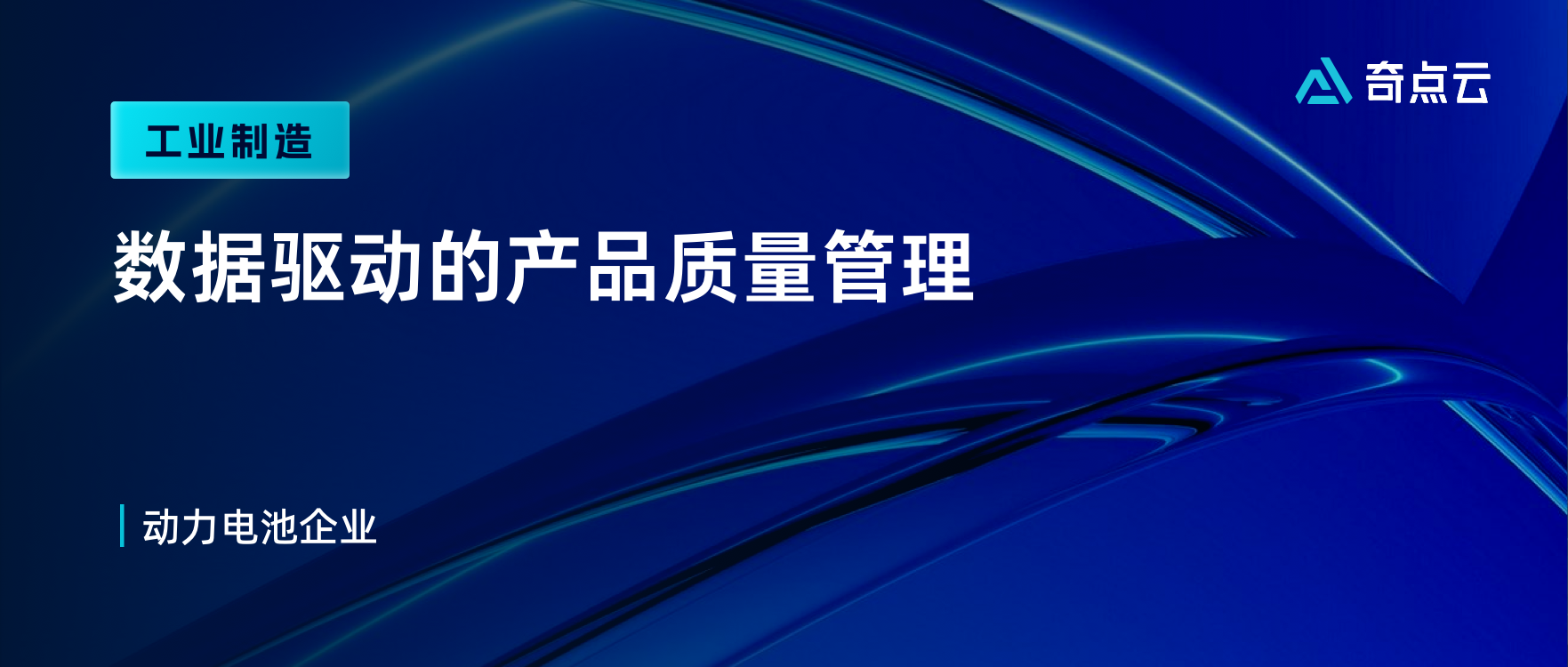
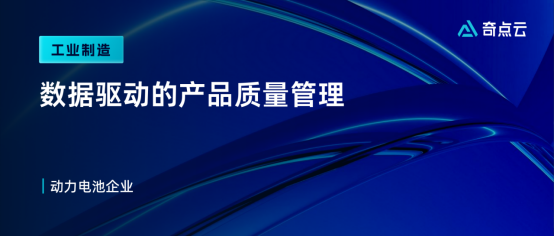
系列导读
如《“数据要素×”三年行动计划(2024—2026 年)》指出,工业制造是“数据要素×”的关键领域之一。如何发挥海量数据资源、丰富应用场景等多重优势,以数据流引领技术流、资金流、人才流、物资流,对于制造企业而言是挑战更是机会。
奇点云梳理了与制造业多个细分领域客户的合作实践,逐篇呈现。本篇以动力电池企业为例,分享数据驱动的产品质量管理优化。
一、背景:动力电池制造工艺复杂,提升产品质量是关键
动力电池是新能源汽车的核心部件之一,其质量对整车的续航和安全性有至关重要的影响。
然而,动力电池的制造工艺非常复杂,涉及多种材料的选择、电池组件的精确装配及封装密封等多个环节。在这个高度专业化和技术密集的领域,如何持续、有效地改进工艺流程,优化材料选用,加强质量控制和检测手段,以保障产品的稳定性、可靠性和耐久性,是业内企业面临的难题,也被视为提升核心竞争力的关键。
与此同时,伴随生产设备自动化程度的提高和工厂物联网建设的完善,海量数据产生,带来了新的机会——如果能基于实时数据完成质量分析与过程控制,变人工判断为数据分析,改手工为自动化,前述问题或将得到高效解决。
二、需求:实现全面、透明、实时、自动化的质量管理
1. 数据层面:海量 IoT 数据,如何高效分析利用?
企业的工业设备、传感器、监控器等系统包含了大量的实时、历史和运营过程相关的信息,例如设备状态、工艺参数、能源消耗、生产指标、故障报警等。
基于对这些数据的分析和挖掘,企业可以发现隐藏在数据中的趋势与关联性,洞察出生产过程中质量的异常情况,及时纠错,优化管理。
然而,不同于传统、相对有限的结构化数据处理,海量 IoT 数据需要现代的数据技术栈提供稳定的存算支持;进一步,需要构建有效的数据模型,持续产出对指导生产有用的分析洞察结果。
2. 业务层面:如何实现质量异常诊断的全面、实时、自动化?如何建立完善的质量管理机制?
传统的动力电池企业往往需要人工统计和操作来进行生产质量管控。而单纯的人工抽检样品可能受到质检人员个体经验的影响,并存在样本数量有限、人工检验时间长等情况,手工统计各环节的数据也可能出现采集不及时、数据录入有误、数据全面度不足等问题。
因此具体到数据应用,企业最直接的目标是用全面、实时的数据实现自动化诊断,保证产品质量稳定性、一致性。
进一步,企业希望通过沉淀、拉通生产全过程数据,实现质量管理透明化,建立并持续完善质量管理的机制。
世界各国对动力电池均设有严格的技术标准和认证体系。在国家和行业标准的指导下,企业需通过质量管理机制,确保从质量问题发现、分析、纠正、预防等各环节可执行,并对质量管理活动进行评估和改进,形成闭环、稳定、有效运作的质量管理,为生产制程的稳定性和质量水平做保障。
三、方案:基于统一底座,建立质量分析模型和闭环管理机制
下文以一家年产能规模近百 GWh 的锂电池制造企业为例,分享奇点云与客户的解决方案和实践。
1. 建立统一的数据平台底座,支持海量 IoT 数据集成处理
生产设备产生的数据量大且复杂度高,包括结构化、非结构化的数据类型及时序等多元化数据结构,基于这些数据进行的业务分析需求也较为多元、动态。因此数据基础设施在设计时必须考虑数据的高效集成和存算,支持业务需求秒级响应。
奇点云以数据云平台 DataSimba 为平台底座,并改造了企业设备通信协议,增加设备数据采集服务器,整体优化了企业的数据基础设施,从而完成对海量 IoT 数据的统一采集、计算、存储及统一规范管理,大大减少线下人工统计带来的干预,提高数据的实时性、一致性和完整性。
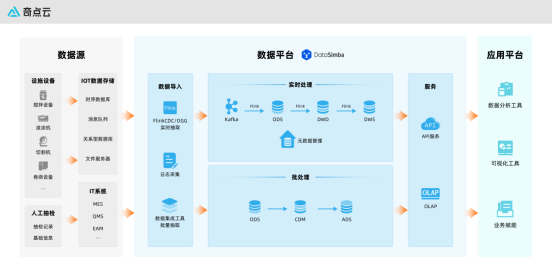
图:基于 DataSimba 构建的企业级数据基础设施
2. 搭建生产过程的质量分析模型,对异常情况实时预警
基于六西格玛、统计过程控制和控制图等过程质量控制方法,搭建生产过程质量分析模型,对 DataSimba 实时采集的数据进行处理,来识别潜在的质量问题和异常情况。
进一步,结合现场生产指挥大屏,以及邮件、短信、OA、钉钉等方式的预警通知,实现对监控生产异常的实时监控、告警和处理,大大减少从发现异常到纠正措施执行的时长。
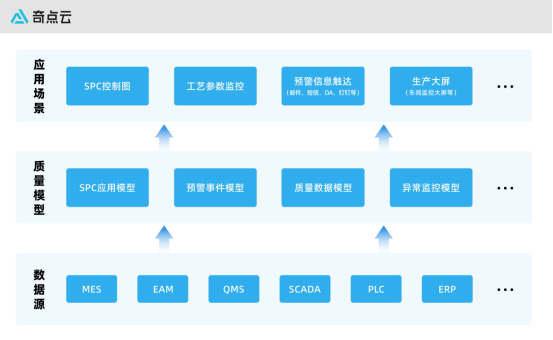
图:数据模型及应用场景简化示意
3. 沉淀产品质量主题的数据资产,建立质量闭环管理机制
沉淀数据资产,是建立产品质量闭环管理机制的前提。但出于设备采集仪器不够精准、设备年限较长、设备故障、环境变化、管理不当等种种原因,企业常常遇到数据质量和数据准确性欠缺的问题,就需要先把通过数据治理和清洗将“资源”转化为具备准确性、完整性、一致性的“资产”,再进行数据的分析和应用。
在产品质量主题的数据资产基础上,奇点云与客户协同应用了 PDCA 循环的质量闭环管理机制,提升质量分析和处理的时效性,确保质量问题得到系统性改善,避免同样的问题再次发生。
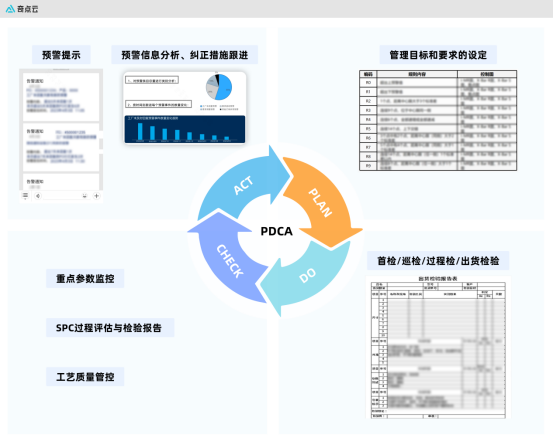
图:PDCA 循环的质量闭环管理图
具体而言,包括:
· P(Plan,计划):以目标为中心,设定质量控制等目标,规定预警触发规则。
· D(Do,执行):以执行为中心,进行检验任务触发、检验任务执行等工作。
· C(Check,检查):以数据为中心,进行对重点参数的监控、分析制程能力等处理。
· A(Act,行动):以问题为中心,采取异常问题纠正与预防措施。
四、价值:用数据还原生产,异常改善率达 100%
1. 提升数据分析的时效性,自动化分析并预警
在该项目实践中,奇点云助力客户完成质量业务运营节点和关键流程节点的梳理,沉淀了产品质量主体的数据资产,搭建了生产质量指标体系和质量分析模型,从而实现生产质量管控从原本的“线下手工统计”转变为“实时线上分析与决策”。
客户数据团队表示,“原本在重点参数监控管理上需要花费 80%的时间去收集和处理数据,只剩 20%时间来进行问题分析和定位,现在数据处理的耗时至少缩减了 75%,有更多的时间来聚焦数据分析,优化场景应用。”
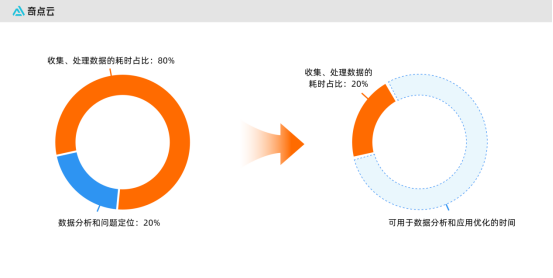
2. 提升质量管理水平,改事后处理为事前、事中、事后的全流程分析
以数据资产为基础,项目对生产过程完成了实时模拟和计算复盘,不仅满足了企业基本的质量管理机制要求,还将原来的“事后分析处理”升级为“事前预测和准备+事中预警和纠正+事后追踪和分析”,实现生产全过程的实时异常改善。在客户为期 3 个月的试跑中,异常改善率达 100%,让企业对质量管理更精细、准确、可靠,也找到了产品质量提升的更大空间。
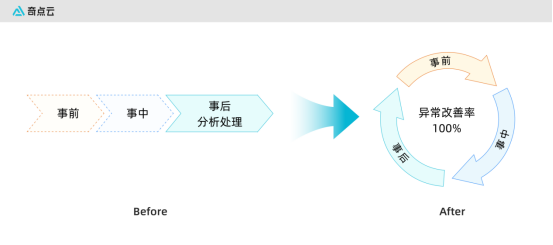
版权声明: 本文为 InfoQ 作者【奇点云】的原创文章。
原文链接:【http://xie.infoq.cn/article/fb1dfc2115ae840b4bff4697d】。未经作者许可,禁止转载。
评论