生产物料管理混乱怎么办?一文教你搞清 BOM 清单和 MRP 需求!
在生产制造的战场上,物料就是后勤补给线,“兵马未动粮草先行”更是能彰显补给的重要性,这是确保整个战局的稳定,如果物料出现问题,别提生产计划了,就连保证基础的生产也会漏洞百出。
物料管理“乱成一锅粥”?先看看这些扎心现场
工人拿着工单,在仓库里翻箱倒柜,半小时过去,还在抓耳挠腮,关键物料却还没着落,生产线只能被迫停工。好不容易找到了,却发现型号不对,又得重新寻找,工期就这样被白白耽误,工人累得直叹气,管理者急得直跺脚。
库存管理更是让人头疼,这边仓库里积压了大量用不上的物料,占用着巨额资金和仓储空间;那边生产线上突然发现缺少核心零件,不得不紧急采购。加急订单不仅价格昂贵,还可能因为物流等问题无法及时到货,导致整个生产进度滞后,成本也随之飙升。
生产计划在这样的混乱中,成了最不靠谱的一张白纸。原计划本周交付的产品,因为物料问题一拖再拖,客户的投诉电话一个接一个...
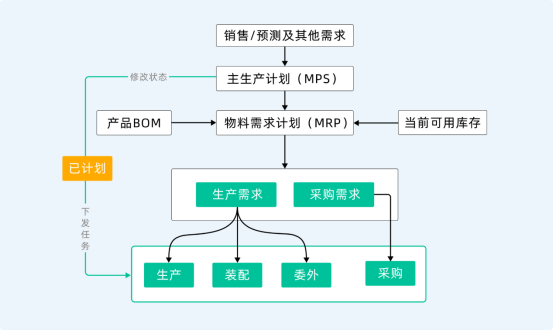
救命神器 1 号:BOM 清单
简单来说,BOM 清单(Bill of Materials)就是产品的 “配方表”,详细记录了生产一个产品需要哪些物料、每个物料的用量是多少,以及它们之间的组装关系。
BOM 清单就是生产领域的说明书。它清晰地列出了从原材料到成品的所有组成部分,让生产过程有章可循。
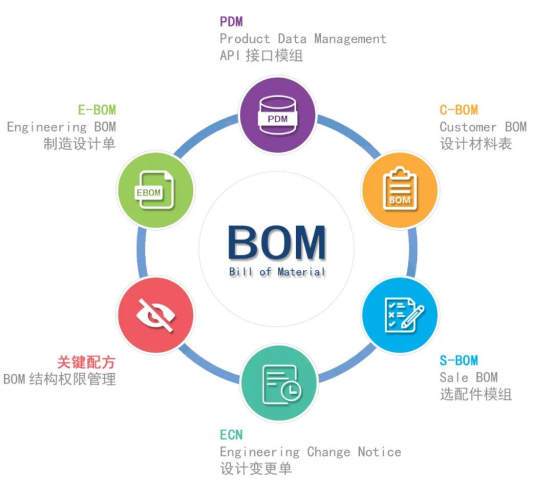
BOM 清单的 3 种核心类型
工程 BOM(EBOM):这是产品设计阶段的 BOM,由设计部门创建,主要关注产品的功能和结构,详细记录产品的所有零部件及其设计关系,是后续生产制造的基础。
制造 BOM(MBOM):进入生产阶段,MBOM 就登场了。它在 EBOM 的基础上,结合了生产工艺和制造流程,增加了生产过程中的工序信息、装配顺序等内容。
销售 BOM:从销售和客户的角度出发,销售 BOM 展示的是产品对外销售的配置和包装信息。
搭建 BOM 清单的 5 个步骤
收集数据:从设计图纸、工艺文件、采购清单等多渠道收集产品相关的物料信息,确保数据的完整性和准确性。
梳理结构:按照产品的功能和组装关系,梳理出物料的层级结构,确定哪些是直接组成部分,哪些是子部件。
录入信息:将收集到的物料名称、规格型号、用量、供应商等信息,准确录入到 BOM 清单中。
审核校对:组织设计、生产、采购等多部门人员,对 BOM 清单进行审核,检查是否存在错误或遗漏。
版本管理:随着产品的升级和工艺的改进,及时更新 BOM 清单,并做好版本记录,确保生产使用的是最新、正确的版本。
救命神器 2 号:MRP 需求
MRP(Material Requirements Planning)即物料需求计划,它的核心逻辑就像超市的补货系统,物料哪里少了,补!物料多了,做出控制!既满足生产需求,又不会造成库存积压。在生产中,MRP 也是通过分析产品的生产计划、现有库存和物料的采购提前期,计算出每个物料的需求时间和数量,确保生产过程中物料及时供应,避免缺料和积压。
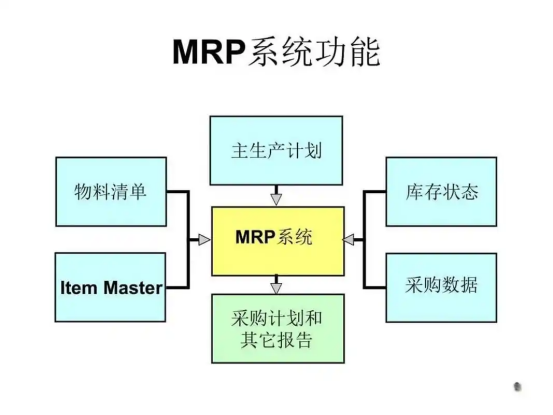
MRP 计算三要素
需求:根据销售订单、市场预测等确定产品的生产数量和时间,这是 MRP 计算的起点。如果需求预测不准确,后续的物料计划也会出错。
库存:实时准确的库存信息至关重要。包括原材料库存、在制品库存和成品库存,只有清楚知道库存有多少,才能计算出还需要采购多少物料。
采购提前期:从下单采购到物料入库的时间,不同的物料采购提前期不同。比如进口的特殊零部件,采购提前期可能长达几个月,而本地采购的通用物料,可能只需要几天。准确掌握采购提前期,才能合理安排采购计划。
从 Excel 到 ERP:不同规模企业的 MRP 落地方案
对于中小企业来说,初期可以使用 Excel 搭建简单的 MRP 模型,通过设置公式和表格,手动输入需求、库存等数据进行计算。虽然效率相对较低,但成本也低,适合业务规模较小、数据量不大的企业。
企业不断发展,可以选择轻量级的 ERP 系统,这些系统集成了 MRP 功能,能够实现数据的自动采集和计算,提高工作效率和准确性。对于大型企业,则需要功能强大、高度集成的 ERP 系统,满足复杂的生产和管理需求。
从混乱到有序:BOM+MRP
第一步:BOM 与 MRP 数据打通的关键操作
要发挥 BOM 和 MRP 的最大威力,首先要实现两者的数据打通。将 BOM 清单中的物料信息、用量等数据,准确导入到 MRP 系统中,确保 MRP 系统能够基于正确的 BOM 数据进行需求计算。同时,MRP 系统计算出的物料采购计划、生产计划等数据,也需要反馈到 BOM 清单中,以便及时调整 BOM 的版本和信息。
第二步:用 MRP 反推 BOM 优化点
通过 MRP 系统的运行,分析物料的需求和使用情况,可以发现 BOM 清单中存在的问题。比如,某些物料频繁出现积压,可能是 BOM 清单中用量设置不合理;某些物料总是紧急采购,可能是 BOM 清单中没有考虑到合理的安全库存。根据 MRP 的分析结果,对 BOM 清单进行优化,砍掉冗余物料,调整用量和结构,提高生产效率和成本控制能力。
第三步:建立动态监控机制
设置缺料和积压预警阈值,当 MRP 系统计算出的物料需求接近或超过阈值时,及时发出预警。例如,当某种物料的库存低于安全库存的 120% 时,系统自动提醒采购部门补货;当某种物料的库存积压超过一定时间或数量时,提醒相关部门进行处理。通过动态监控机制,实时掌握物料的供需情况,及时采取措施,避免缺料和积压问题的发生。
别让好工具变“摆设”
常见误区:认为有系统就万事大吉
很多企业引入 BOM 和 MRP 系统后,以为问题就能迎刃而解,却忽略了系统的日常维护和管理。实际上,系统只是工具,关键在于人的使用和管理。如果不及时更新数据、不严格执行操作流程,再好的系统也无法发挥作用。
数据准确性的“生命线”:定期核查与维护
BOM 清单和 MRP 系统的数据准确性至关重要。每周或每月定期对库存进行盘点,核对 BOM 清单中的物料信息和用量,确保与实际情况一致。及时更新采购提前期、供应商信息等数据,保证 MRP 计算的准确性。
评论