设备维修不是单纯的修机器,这五个方面一定要清楚!
设备维修绝不是简单的零件更换与故障排除,当企业盲目将维修等同于“修机器” 时,往往会陷入效率低下、成本攀升的恶性循环。真正的设备维修,是涵盖技术诊断、全生命周期管理、生产协同、人员培养和成本优化的系统性工程。
设备维修的本质认知
传统认知的局限与弊端
传统观念中,设备维修似乎就是“哪里坏了修哪里”—— 电机不转就换轴承,管道泄漏就补焊接口。某食品加工厂曾因包装机传送带断裂紧急停机,维修人员仅更换皮带后便重启设备,却在三天后因驱动轮磨损不均导致二次故障。这种 “头痛医头,脚痛医脚” 的做法,不仅造成重复维修成本,更让生产线陷入 “被动救火” 的困局。
现代设备维修的系统性定义
事实上,现代设备维修早已突破物理修复的范畴。以汽车发动机为例,其故障可能源于传感器信号失真、ECU 程序异常或油路积碳,单一的机械检修根本无法触及问题本质。真正的维修,是从设备功能、性能和可靠性出发,将机械结构、电气系统、自动化控制乃至环境因素纳入统一框架。这充分证明:设备维修是保障生产系统稳定运行的核心环节,唯有系统性思维,才能实现 “长治久安”。
核心维度一:技术诊断能力的深度构建
故障溯源逻辑:从表象到根源
真正的技术诊断,必须穿透故障表象,找到引发问题的根本原因。
现代维修已形成“5Why 分析法”“鱼骨图” 等系统化工具。例如,当数控机床出现加工精度偏差时,通过连续追问 “为什么尺寸超差?→刀具磨损→进给速度不均→伺服电机参数异常→编码器信号干扰”,最终定位到电磁屏蔽不足的设计缺陷。这种抽丝剥茧的思维方式,配合振动频谱分析、油液铁谱检测等先进技术,能将故障定位精度提升至毫米级甚至微米级。
在智能制造时代,设备早已成为多学科技术的综合体。以工业机器人为例,其维修不仅涉及机械传动和液压系统,更需掌握伺服电机控制算法、视觉识别程序调试以及通信协议解析。这要求维修人员必须构建“T 型知识结构”—— 在精通某一领域的基础上,横向拓展自动化、材料科学、数据分析等跨学科知识。
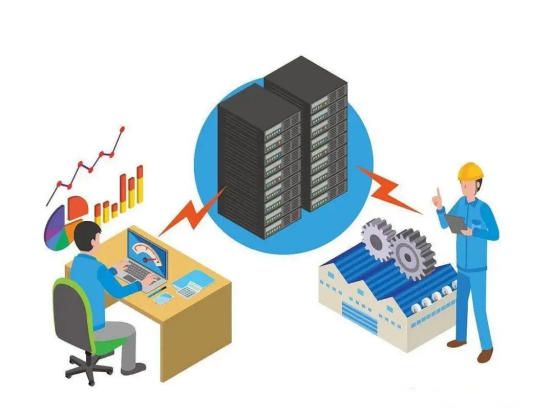
核心维度二:设备全生命周期的协同管理
前期预防:防患于未然
设备的健康状态,从安装调试阶段就已注定。预防性维护应从设备选型、安装调试阶段开始,制定基于工况的预测性维护计划。例如,根据设备运行时长、温度曲线和历史故障数据,提前储备易损件,将定期更换改为状态监测下的按需更换。
中期运维:经验沉淀与优化
建立维修知识库是提升效率的关键。某钢铁企业通过数字化平台记录 10 万 + 条维修案例,当高炉鼓风机出现喘振时,系统自动匹配历史解决方案,将故障处理时间从 4 小时缩短至 40 分钟。
后期迭代:从问题中学习
维修数据是设备改进的金矿。某工程机械制造商在处理 100 + 起挖掘机液压管路爆裂故障后,发现 70% 问题源于设计缺陷,通过优化管路走向和接口材质,使同类故障下降 90%。这种 “维修 - 反馈 - 改进” 的闭环机制,不仅能降低故障率,更能推动产品设计升级。
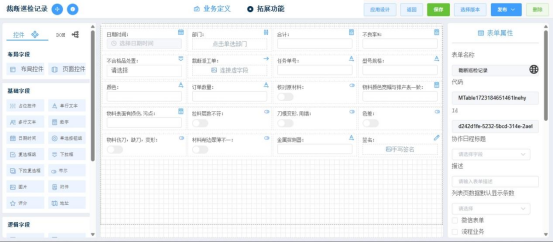
核心维度三:生产流程与维修的动态匹配
维修对流程的反哺
维修数据能为生产优化提供关键线索。某汽车冲压车间发现压力机模具更换频率异常,经分析维修记录发现是原材料厚度波动导致模具磨损加剧。通过与供应商协同改进来料标准,模具寿命延长 3 倍,换模时间缩短 50%。这种 “维修 - 生产 - 工艺” 的联动机制,使设备维护从成本中心转变为价值创造中心。
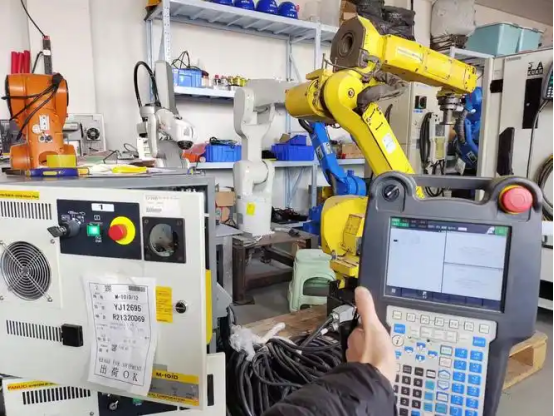
核心维度四:人员能力与管理体系支撑
维修团队能力模型:从“技工” 到 “工程师”
传统维修人员的“经验主义” 正逐渐被淘汰。某新能源车企要求维修技师掌握 Python 数据分析、MATLAB 仿真建模等技能,以便解析电池管理系统的复杂故障。企业通过 “技能矩阵 + 项目制培养” 模式,将普通维修工培养成能独立解决智能产线故障的复合型人才。同时,跨部门协作能力成为必修课 —— 维修人员需与工艺工程师共同优化设备参数,与 IT 团队对接工业互联网平台。
管理体系搭建:让流程说话
标准化流程的价值
标准化流程是设备管理的“隐形翅膀”。某食品饮料企业通过 ISO 55000 资产管理体系认证,建立从采购验收、日常点检到报废处置的全流程标准,设备综合效率(OEE)提升至 85%。
数字化工具的赋能
数字化工具的应用更为管理赋能:引入 CMMS 系统后,备件库存周转率提高 3 倍,维修工单响应时间缩短至 15 分钟。这些成果证明:科学的管理体系能将个人经验转化为组织能力,让设备管理告别 “人治” 走向 “法治”。
核心维度五:成本与价值的全局考量
短期成本控制:避免“过度维修”
“维修万能论” 往往导致资源浪费。某造纸厂曾因担心压榨辊磨损,每季度更换轴承,后经状态监测发现轴承寿命可达两年,年节约备件成本 120 万元。企业需建立 “风险 - 成本” 评估模型,区分安全相关的必要性维修(如压力容器检测)与非关键部件的非必要性升级(如过早更换磨损未超限的皮带)。
长期价值创造:从成本中心到利润引擎
设备维修的终极目标是创造价值。某家电企业通过优化空调生产线的预防性维护策略,将设备综合效率从 72% 提升至 88%,年产能增加 50 万台,直接创造利润超 3000 万元。这种价值转化不仅体现在产能提升,更包括能耗降低、质量改善和品牌溢价。当维修部门能通过数据证明 “每投入 1 元维护成本可带来 3 元收益” 时,其战略地位将得到根本性改变。
结语:从“被动修” 到 “主动管” 的思维转型
设备维修的本质,是用技术与管理的力量重构生产秩序。当企业将维修视为系统工程,而非孤立任务;当维修人员从“救火队员” 转型为 “系统设计师”;当数据与流程成为决策核心,设备将不再是成本负担,而是价值创造的 “永动机”。未来的工业竞争,不仅是生产效率的比拼,更是设备管理智慧的较量。唯有拥抱系统性思维,才能在智能制造的浪潮中占据先机。
评论