设备健康管理“悬丝诊脉”之【石化行业往复式压缩机】
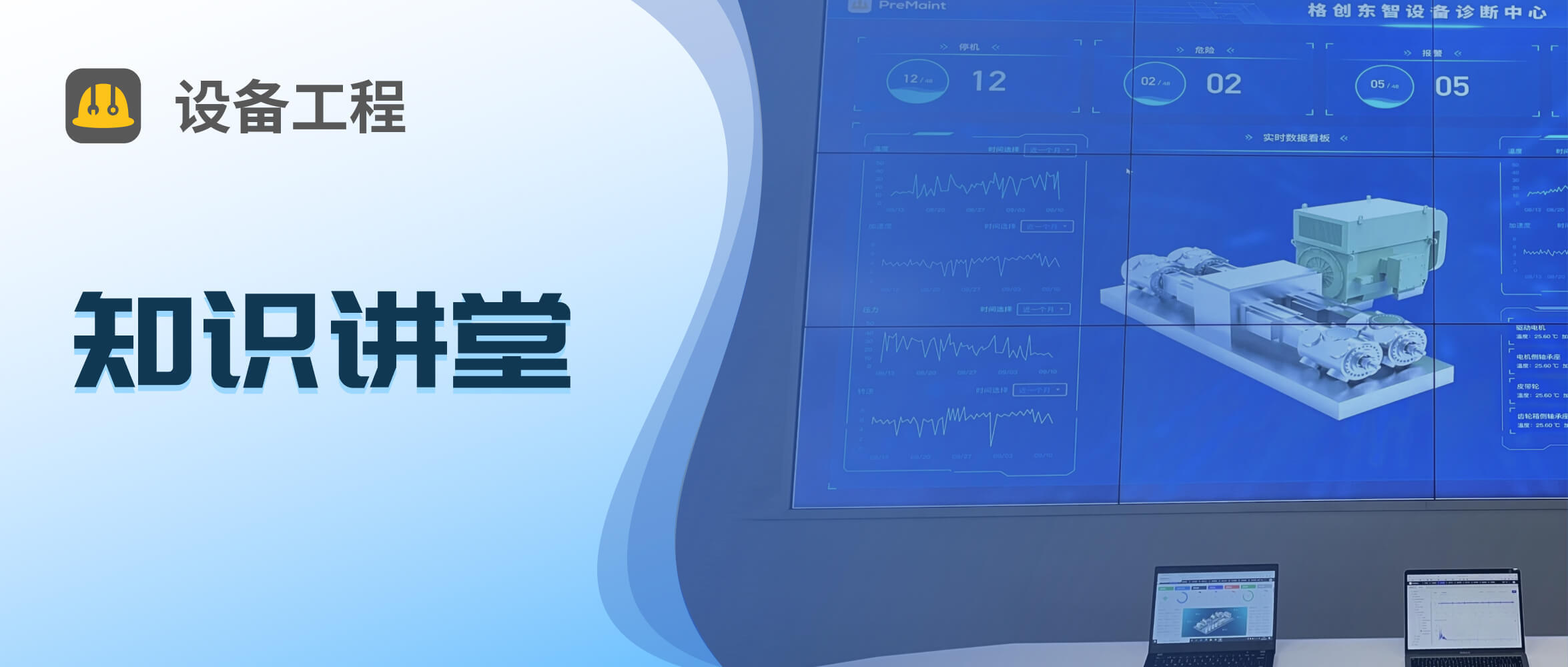
诊脉是中医断病的一个重要途径。在古装剧里,我们时常能看到太医通过一根线为尊讳者“诊脉”,就是所谓的“悬丝诊脉”。工业设备同样由各种动、静部件构成,如果设备“带病”运行,我们能否通过设备的“脉象”为设备诊断呢?本文我们将化身设备健康医生来为石化行业的往复式压缩机做一个全面的“悬丝诊脉”。
文章来源
格创东智 PreMaint 资深解决方案专家-王鹏
介绍:中国设备工程专家库专家,天津市科协会员。拥有 17 年的石油化工、冶金矿山、电力能源等行业工业设备管理及运维经验,具有丰富的工业互联网平台咨询、行业解决方案及项目实施交付经验。
01 “病人”-往复式压缩机
往复式压缩机凭借热效率高、技术成熟、适用压力范围广等诸多特点,在生产作业流程中广泛应用,主要用于加氢、重整、原料气、集输、燃气透平燃料供给等装置。
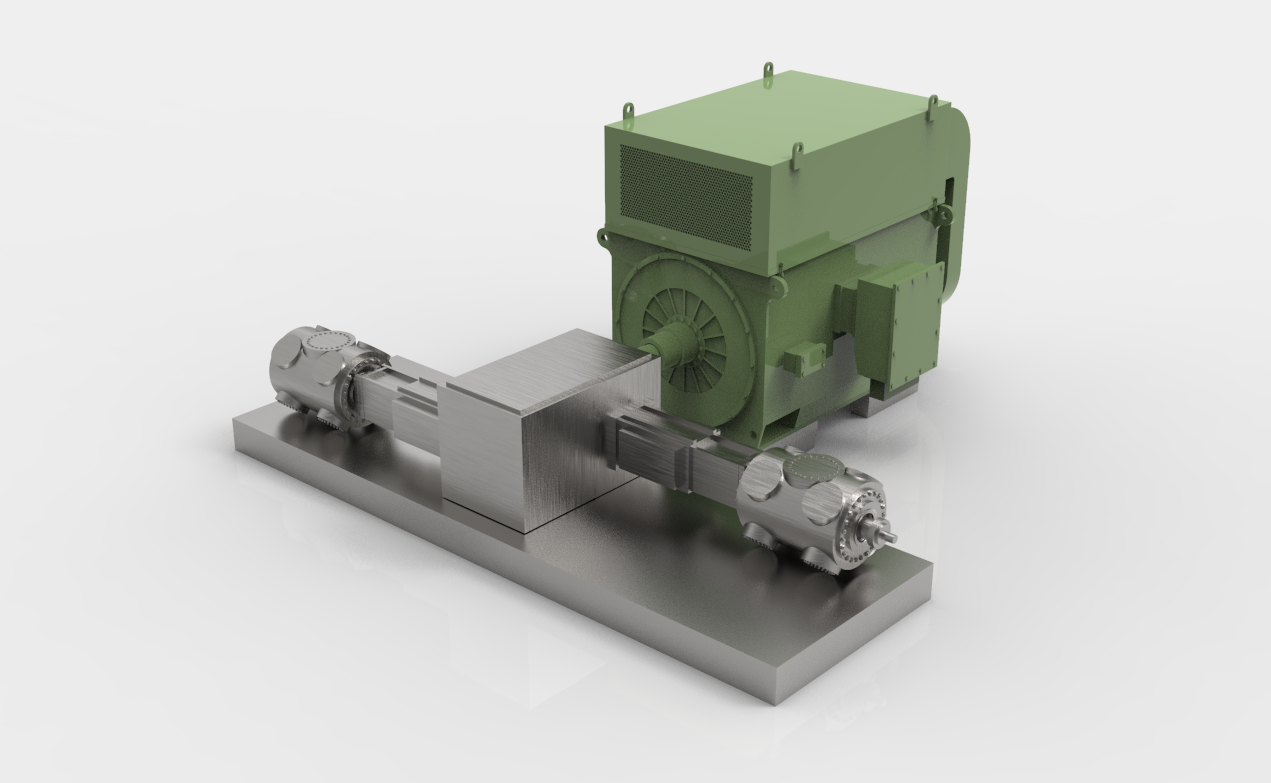
图.往复式压缩机整体图示
往复式压缩机在石化生产领域发挥着极为重要的作用,运转状况关系到整个生产流程。如果运行中的压缩机出现非计划性停车,将导致一系列问题:影响工艺流程、造成巨大的生产损失、增加额外的维修费用、影响人员、环境及设备安全等。研究表明 80%的非计划性停车是由于气阀、活塞/活塞杆、填料、活塞环/支承环故障引起的。
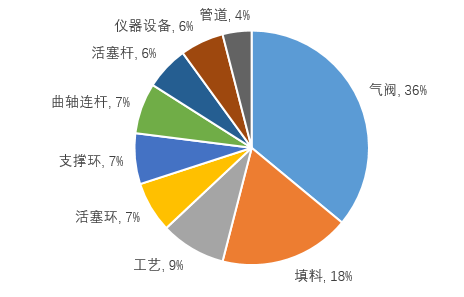
图. 往复式压缩机常见故障占比
为了提前发现以上故障,防患于未然,减少意外停机和灾难性事故,保证设备长周期、安全稳定运行,我们可通过对往复式压缩机进行“悬丝诊脉”,提前发现设备的亚健康状态。
02 “悬丝”-多源数据采集
我们通过物联网技术连接现场设备,采集与故障诊断分析相关的数据。数据采集多源性的选择往往与设备运动特性和激励信号机理有很大关系。由于往复式压缩机需要利用一系列机构将回转运动转换成往复运动,因而其机械结构往往比较复杂,运动形式也较为复杂。冲击、漏气和摩擦是往复式压缩机最主要的信号类型,其在时域的特征如图所示。
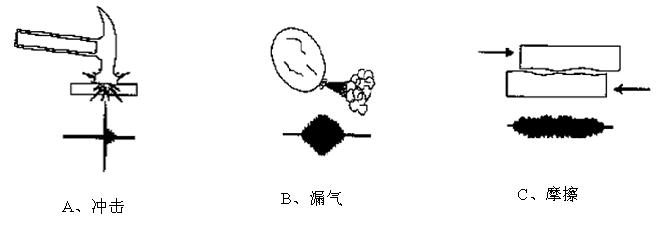
图. 冲击、漏气和摩擦时域的特征
另外,往复式压缩机与旋转机械相比,有以下特点:
(1)系统比较复杂,运动部分(曲轴—连杆—活塞)既有旋转运动引起的振动,又有往复运动产生的振动,还有进排气时冲击造成的振动,众多的频率,范围广泛的激励力比较难以识别。
(2)振动随负荷变化,在转速一定时,其负荷又随外界情况变化。
(3)同时发生多种振动,如进排气引起气阀组件的振动,活塞撞击连杆瓦引起的振动,活塞摩擦气缸引起的振动等几乎在同一时刻发生。因此相互干扰大,当压缩机的运动部件出现不同构件的机械故障时,难以从单一振动信号中捡出相应的激励力变化情况。
(4)各种撞击力大小都具有不稳定性。
(5)缸数多,互相耦合,相互干扰,邻缸对本缸以及本缸中各运动部件之间的互相干扰不易区分。
键相信号可以辅助振动频率成分分析和相位分析,动态压力信号可以通过算法处理来辅助分析热力性能故障和机械性能故障。所以我们通常结合基于转角相位分析的振动信号采集和动态压力数据采集来解决上述问题。设备现场数据采集包括加速度信号、电涡流位移信号、动态压力信号、键相信号等。
03 “诊脉”-远程诊断分析
设备现场采集到的多源数据通过网络传输到远程诊断中心,在中心室基于 PreMaint 设备健康管理平台可以实时监测设备数据,通过诊断分析工具来实时评估设备健康状态真正实现“悬丝诊脉”。
PreMaint 具备综合故障诊断及健康评估能力,基于采集每一个做功周期的气缸压力曲线和阀盖的振动波形以及温度数据,使压缩机的膨胀、吸气、压缩、排气事件与气阀的启闭事件对应起来,同时也使气阀的故障信息在曲线上清晰地显露出来。基于活塞杆受力曲线图结合相位振动综合分析,可以对包括十字头、大小头瓦、活塞锁母松动等故障进行分析。基于活塞杆沉降、偏摆位移监测可以对活塞磨损、活塞杆磨损、填料函磨损、十字头间隙异常等故障作出有效分析评估。
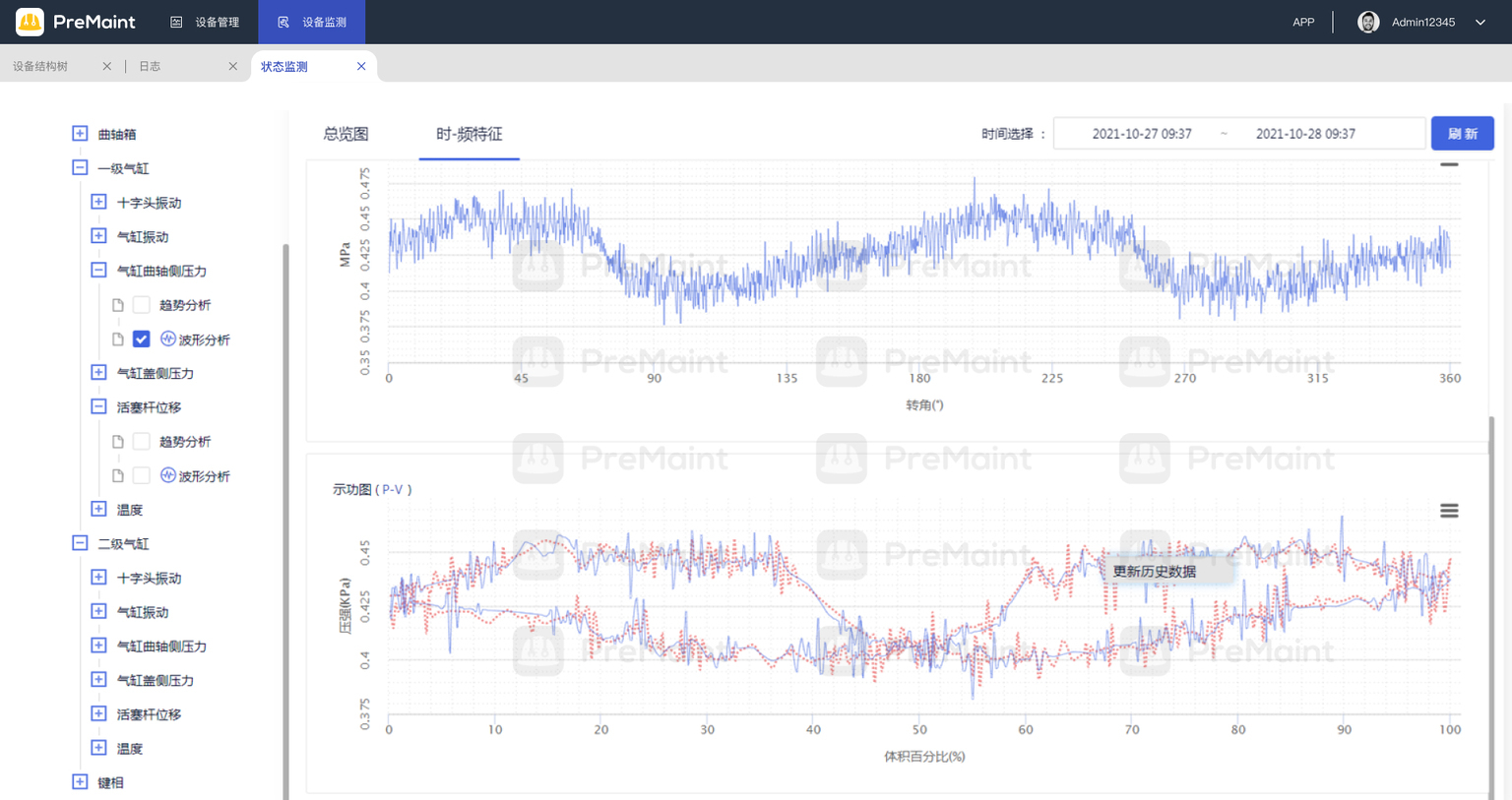
图.气缸压力曲线和阀盖的振动波形
以连杆大头瓦磨损故障分析为例,对于双作用压缩机,活塞杆受力由作用在活塞两侧的气体压力差,活塞、活塞杆、十字头、连杆产生的往复惯性力,活塞环与气缸、十字头与滑轨产生的摩擦力组成。由于气体压力、往复运动组件的加速度是瞬时变化的,活塞杆的受力也随之变化。
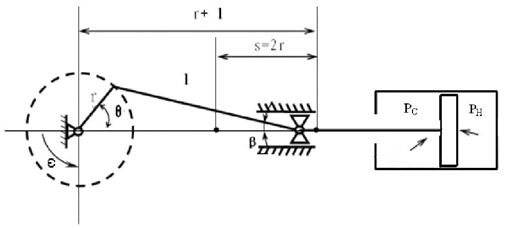
图.曲柄连杆受力示意图
通过采集活塞两侧的压力曲线,计算往复运动组件的往复惯性力,即可得到活塞杆的受力曲线和活塞杆受力反向的角度,API618 标准规定反向角不小于 15°,当十字头销与衬套、曲轴销与连杆大头瓦间隙过大时,在活塞杆受力反向时就会产生冲击,间隙大则冲击的幅值也大。通过压缩机十字头振动曲线分析,与活塞杆受力曲线比较,即可判断连杆大、小头间隙是否正常。
在对压缩机某缸活塞杆受力和十字头振动曲线图分析时发现,活塞杆受力反向时出现幅值异常的冲击幅值。检查发现连杆大头瓦巴氏合金层已磨穿。如果不是及时发现,则可能会造成曲轴磨坏、连杆拉断的重大设备事故。
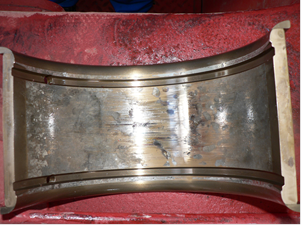
图.异常部位拆解情况
目前石化行业往复式压缩机等设备的运行维护主要以人工巡检、事后维修、定期检修的传统模式实施,无法预防突发恶性故障、无法对设备运行状态进行整体评估,直接影响到设备及生产的可靠性和安全性,不能适应现代化设备管理水平的要求。随着设备运行期增长、可靠性降低、故障率增加、维保及备件费用逐年增加,建设远程监测诊断系统逐渐成为石化企业设备管理提升的必要手段之一。使用 PreMaint,通过“悬丝诊脉”即可实现设备的远程故障诊断和健康管理,提前预知设备裂化趋势,从而达到降本增效和满足设备精细化管理的需求。
版权声明: 本文为 InfoQ 作者【PreMaint】的原创文章。
原文链接:【http://xie.infoq.cn/article/8869c49f88d923571dbe03b70】。文章转载请联系作者。
评论