MyEMS 开源能源管理系统在生产中的核心作用与应用价值
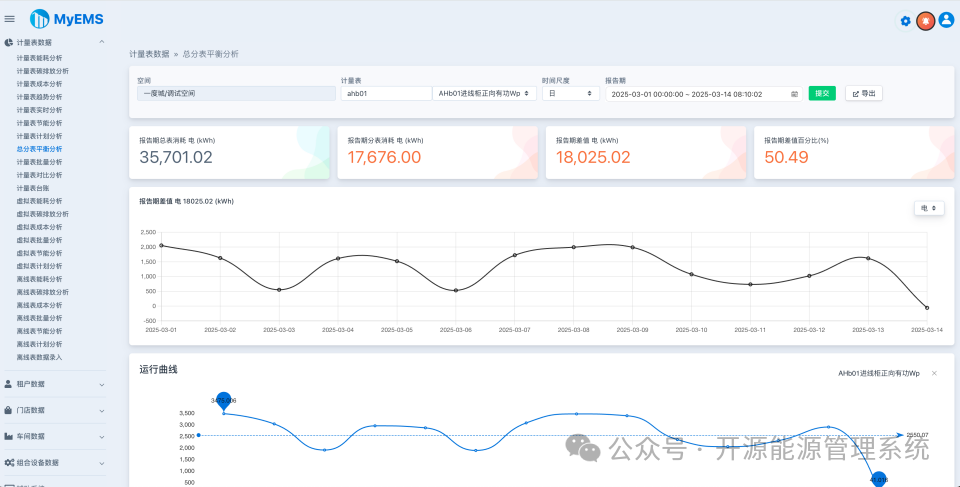
MyEMS(My Energy Management System)作为开源能源管理系统,在生产场景中主要通过数据采集、监控分析、优化控制等功能,帮助企业实现能源消耗的精细化管理,提升能效利用水平。以下是其在生产中的具体作用及应用场景解析:
一、实时能源数据采集与监控,掌握生产能耗动态
多维度数据整合:可对接生产现场的电表、水表、蒸汽流量计、PLC 设备等,实时采集电力、热力、水资源等能源消耗数据,覆盖生产线、车间、设备等不同层级。
可视化监控平台:通过仪表盘、趋势图等可视化界面,展示实时能耗数据、设备运行状态(如负载率、待机能耗),帮助管理人员直观发现高耗能环节(例:某台机床待机功率异常)。
异常预警机制:设定能耗阈值,当设备能耗超出正常范围时(如单位产品耗电量突增),系统自动报警,及时定位生产过程中的能源浪费问题。
二、数据分析与能效优化,降低生产能源成本
能耗模型建立:基于历史生产数据(如产量、能耗、工艺参数),构建能耗分析模型,识别 “能耗 - 产量” 的关联关系,优化生产排程(例:调整设备启停时间,避开用电高峰)。
节能潜力挖掘:通过对比分析不同车间、班次、设备的能耗效率(如 OEE 设备综合效率与能耗的关联),找出低效环节。例如:发现某条产线在夜班的单位能耗比白班高 15%,进而优化夜班生产流程。
工艺优化建议:结合能源数据与生产工艺参数(如温度、压力、转速),提供工艺调整建议。例如:某化工反应釜温度设定降低 5℃,能耗可下降 8%,且不影响产品质量。
三、设备管理与智能控制,提升生产系统能效
设备能效评估:跟踪关键设备(如空压机、制冷机)的能耗效率曲线,自动生成能效报告,辅助设备维护或更新决策(例:淘汰高耗能老旧电机)。
智能负载调度:根据生产计划与能源价格(如峰谷电价),自动调整设备运行策略。例如:在低谷电价时段提前开启储能设备,高峰时段减少电网用电,降低用电成本。
联动控制优化:与 SCADA、MES 系统集成,实现能源与生产流程的联动。例如:当生产线暂停时,系统自动降低辅助设备(如通风机)的运行功率,避免 “空载耗能”。
四、合规性管理与碳足迹追踪,响应政策要求
能源报告自动生成:支持按国家标准(如 GB/T 23331)或行业规范生成能耗报表,满足政府能耗统计、节能审查等合规需求。
碳足迹核算:基于能源消耗数据,自动换算碳排放当量,帮助企业追踪生产过程的碳足迹,为碳交易、碳中和目标提供数据支撑。
ISO 50001 体系支持:系统功能符合能源管理体系标准,可辅助企业建立 PDCA(计划 - 执行 - 检查 - 改进)循环,持续优化能源绩效。
五、开源特性带来的生产适配优势
灵活定制开发:开源代码允许企业根据生产特性(如半导体行业的超净车间能耗管理、钢铁厂的高温设备监控)定制功能模块,适配特殊生产场景。
低成本部署:无需支付闭源系统的授权费用,降低中小企业的能源管理系统建设成本,尤其适合多工厂、多产线的集团化企业。
社区生态支持:依托开源社区的持续迭代,系统可集成最新的能效算法(如 AI 能耗预测模型),及时适配生产技术升级(如新能源设备接入)。
六、典型生产场景应用案例
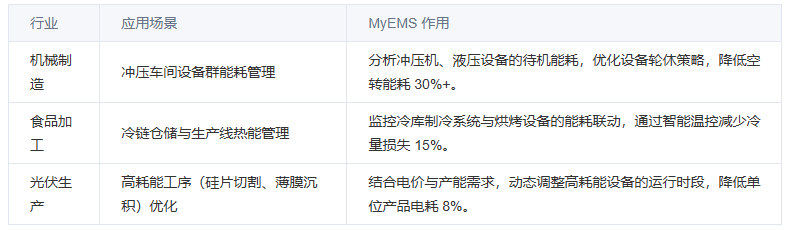
总结:MyEMS 对生产管理的核心价值
MyEMS 通过 “数据驱动 + 智能控制 + 开源灵活” 的特性,将生产中的能源消耗从 “事后统计” 转变为 “实时管控”,不仅帮助企业降低能源成本(通常可实现能耗下降 10%-20%),还能通过能效优化提升生产稳定性,同时满足绿色制造、低碳生产的行业趋势要求。对于追求精细化管理的制造企业,尤其是希望自主掌控能源管理系统适配性的用户,开源架构使其成为兼具性价比与灵活性的解决方案。
评论