工赋开发者社区 | 复杂电子装备制造数字化工厂实现逻辑与实施步骤
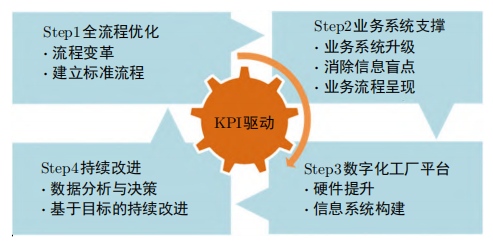
随着国际竞争的不断加剧,对设备效率、制造成本、产品质量等环节的要求不断提高,通过数字化转型、构建数字化工厂来进行产业升级、提质增效,解决现有制造业的困境,成为行业内普遍认可的一种手段。越来越多的企业开始重视并已经开始了数字化转型的工作和部分解决方案。美国波音公司在设计制造中,利用数字化建模技术实现了产品设计与制造环节的信息协同,缩短了设计与制造时间,大幅度降低了飞机成本;大众汽车的斯柯达工厂利用虚拟仿真技术进行工艺路线规划,减少实际生产线的调整和改进,有效缩减非增值环节,提升了生产效率。
实践证明,数字化工厂的解决方案能够帮助制造企业缩短产品上市周期,提高产品质量和生产效率,降低生产成本和故障风险。玛莎拉蒂的 Bertone 工厂通过数字化方法在制造执行过程中同步信息变化,实现柔性化的混线生产,实现不同车型的全自动生产和组装,产能提升超过了 2 倍。
针对小批量、离散型的复杂电子装备制造行业,数字化转型是企业进一步提升的手段之一。通过数字化技术将生产、制造、工艺、人员等进行持续改进优化,减少人为因素的影响,使生产制造过程实现全面要素的精确可控,最终为企业带来全领域质量提升和效益提升。
1.行业现状及存在的问题
因固有的小批量、多品种、短周期特点,在复杂电子装备尤其是雷达电子装备的生产过程中,一直存在着计划排程不准确、物料配送不及时、人员调度困难、设备状态不清楚、交付拖期超期等一系列问题。其中客户的交付需求往往是行业面临的最大挑战,围绕着产品的交付计划,如何完成生产要素的动态整合、生产资料的按需配给,是保障电子装备研制生产和交付的关键。
其实,这一系列问题的根源在于流程繁琐混乱、过程监测匮乏、生产资源不协调以及缺少顶层的决策和管理。支撑决策和管理的根本就是数据,数据是数字化转型的驱动力。数字化转型意味着企业从僵化到敏捷,通过数字化技术疏通整个制造流程,完成人力、物力、资源的协同配合,完成生产过程的透明化管理和质量的监测。但数字化转型是一个系统工程,不仅仅是一台设备自动化的提升、一个环节的数据采集,更是一个全局优化和迭代的过程。
2.数字化工厂的实
现逻辑与实施步骤
企业的关键绩效指标(KPI)也是数字化转型过程的核心驱动力。KPI 可以客观、有效地衡量数字化工厂建设中的因素和变化,将精力从无关紧要的琐事中解脱出来,着重关注数字化工厂实现过程中的关键改善方向,提升改进效果。数字化工厂实现的逻辑与实施可以简单分为 4 个步骤,如图 1 所示。
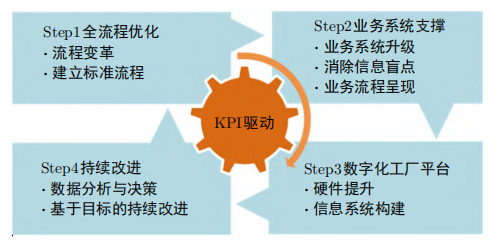
图 1 基于 KPI 驱动的数字化工厂实现逻辑
首先需要通过全流程优化构建数字化的标准流程。通过流程变革,疏通生产过程中的堵塞环节,建立多并行、少环节、快响应、多备份的标准化流程。然后是业务系统的有效支撑。通过捕获企业管理的优先级,对照行业领先做法分析当前绩效,以确定关键绩效差距,并以此为基础确定速效、长期的运营改进和成本降低机会。制定企业优先计划路线图和升级业务系统,通过业务流程再现的方式,梳理业务流程中的问题和改善方向,结合 KPI 指标进行分析,从而解决业务系统中的主要问题。
进一步搭建数字化工厂平台。平台的建立包括车间信息系统的构建以及工厂硬件的提升。以自动化水平提升为依托,构建基于生产数据的制造运营管理力量。瞄准脉动式生产对资源动态调配的需求,建立数据采集、制造运营、仓储物流、运行监测等信息化系统,以数据贯通数字化工厂平台的运行。最后,通过平台呈现的数据,对生产计划进行自动排程,对人员、设备、物料进行动态调配。建设可视化综合看板,进行生产过程的决策和管理,并基于目标完成持续改进,最终实现企业的数字化转型。
本文以一个典型的雷达电子装配为例,通过全流程调研流程呈现、分析与优化和数字化转型路径 3 个维度对复杂电子装备的数字化实现过程进行了探索和研究。
3.复杂电子装备的
全流程调研流程呈现
3.1 从订单到交付
以典型雷达电子装备为例,从订单到交付(OTD)主要包括研发设计、物资采购、生产制造和质量管理 4 个大的层面,具体如图 2 所示。每个层面在产品生产的全生命周期中都存在着一定的问题,而这些问题往往不仅仅是各层面本身的技术问题,更多的是整个生产流程、各个生产环节彼此牵制关联形成的。因此,面向雷达电子装备多品种、小批量、变节拍的柔性生产需求,消除现有生产端的业务痛点与难点,完成数字化转型,首要任务是自上而下全流程梳理与优化。
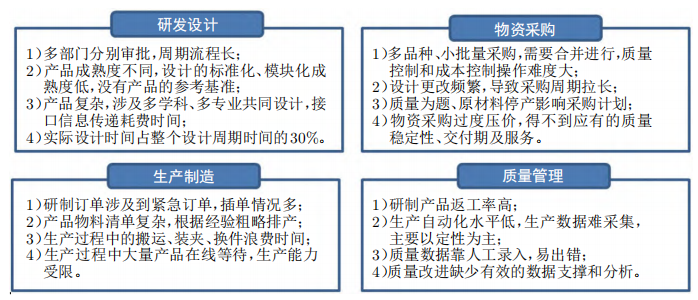
图 2 OTD 过程中的问题汇总
3.2 典型业务流程现状及描述
作为一个复杂的电子装备,从合同签订至产品交付,整个项目周期持续约 22 ~ 25 个月,其整体业务流程及每个子业务的基本流程如图 3 所示。项目实施过程涉及企业内多个部门,审批流程多,周期长。另外,业务过程复杂多变,沟通协调难度大。
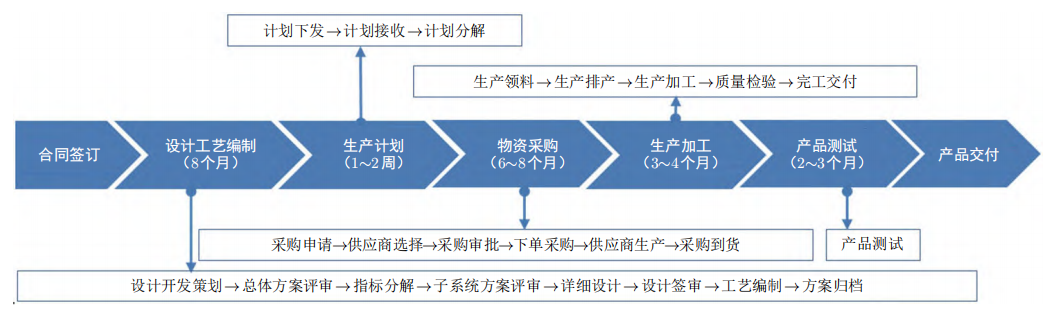
图 3 复杂电子装备的业务流程图
3.3 业务流程存在的问题
1)设计工艺编制
雷达电子装备的设计多是针对新产品的设计,设计的标准化、模块化成熟度低,设计过程中各种影响因素较多,有效的设计时间只占整个设计周期的 30%左右,具体存在的问题及改进方向如图 4 所示。
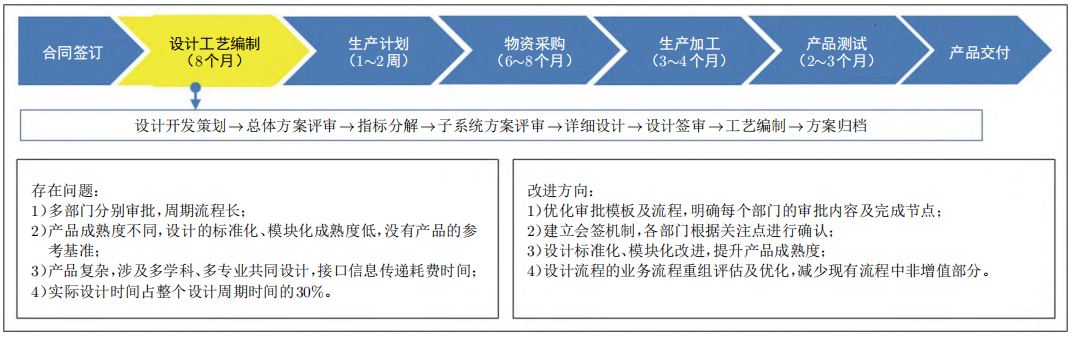
图 4 设计工艺编制存在的问题及建议
2)生产计划、物料采购
多项目混合的物料采购方式给计划的制订带来很大的困难,导致采购难度大,同时原材料问题、设计更改等都会影响物料采购及计划的制订,具体如图 5 所示。
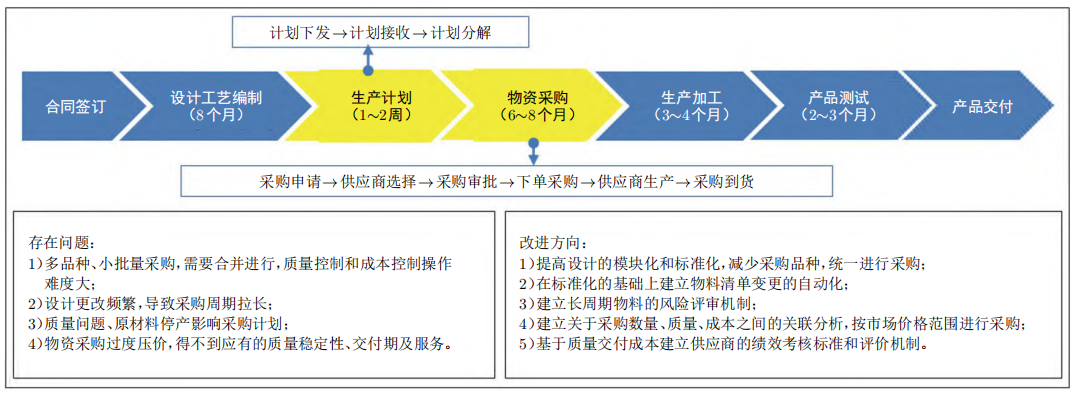
图 5 计划、采购存在的问题及建议
3)生产加工与测试
生产过程中存在紧急订单和较多的插单情况,给生产的均衡进行带来影响。同时,生产过程中无效等待时间较多,限制了生产能力并延长了生产周期,具体如图 6 所示。
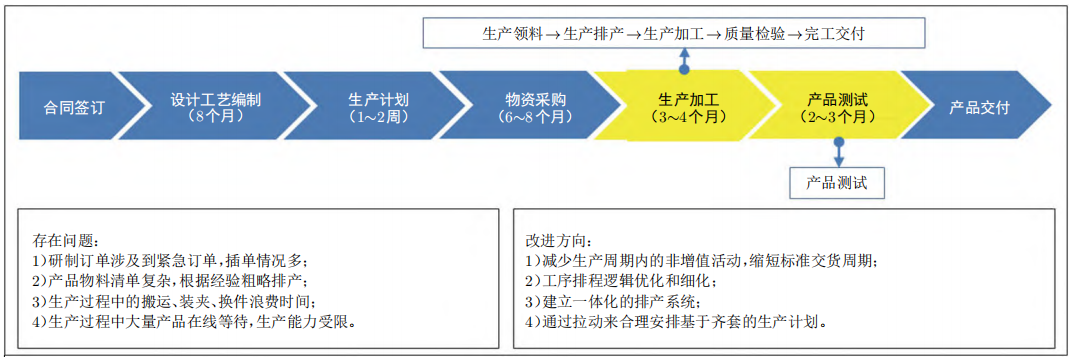
图 6 生产过程存在的问题及建议
4.分析及优化
4.1 业务流程优化
通过对项目过程中各业务流程的问题进行分析,梳理存在的问题,提出改善建议。同时对设计管理、采购管理和制造管理 3 大业务的改善方向及 KPI 指标进行分析,具体见表 1。
表 1 项目改善方向及 KPI 指标
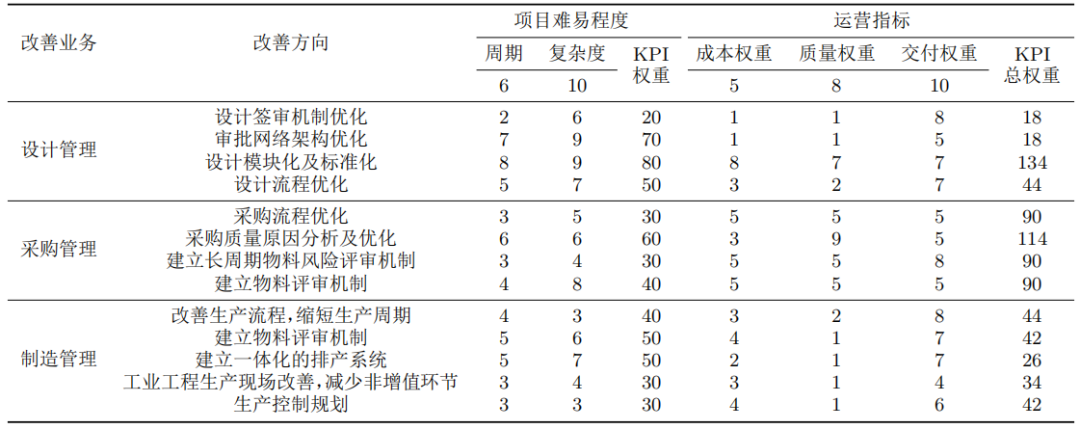
通过对业务过程的改善方向权重进行分析,形成问题改善地图,如图 7 所示。根据图 7 所示的问题改善地图可以找出项目难度低且 KPI 指标高的改进项,作为首要改进目标来实施,按照评价等级 1—4,逐步突破,将问题全部解决从而提升企业效率。
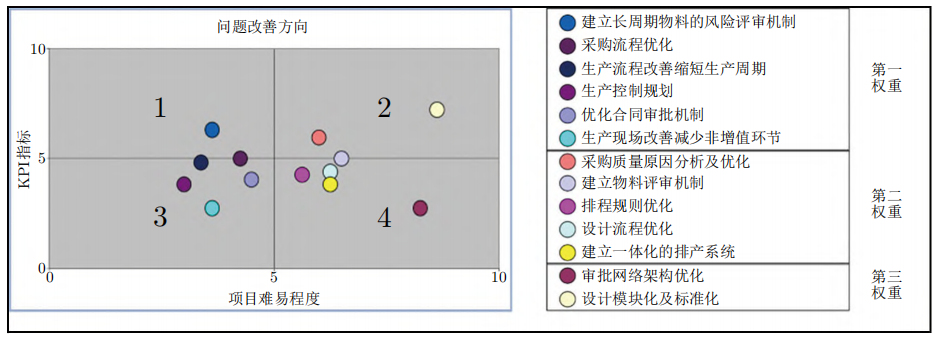
图 7 问题改善地图
4.2 质量管理优化
从合同签订到产品交付,质量管理贯穿整个业务过程,每个环节都存在质量管控点。质量体系、质量控制及质量改善是企业质量管理的核心工作。数字化工厂建设相关工作主要是寻找信息化的潜在支撑,对质量问题及数据予以呈现。
对于图 2 所示产品交付过程中的问题,数字化对质量改善的建议包括:1)针对研制产品返工率高的问题,记录返工流程,为系统性分析提供依据;2)在过程质量控制(PQC)方面,推进数字化装配工具应用,消除信息盲点,完善质量数据;3)针对质量数据多以定性为主、人工输入占比较大,导致质量改善缺少有效的数据支撑和分析的问题,提升过程自动化检测水平,通过设备检测数据的自动采集和结构化存储,来支撑质量数据的录入及统计分析。
5.数字化工厂建设
5.1 数字车间建设
数字车间建设主要围绕工艺流程、生产装备、生产效率、物流效率等方面开展。针对制造过程、检验过程和测试过程,合理优化工艺流程,均衡各工位生产节拍。开展生产装备自动化建设,通过给各工位配备自动化工装和设备,提升装备专业化水准,实现各工位的效率提升。以智能、柔性生产线为依托,根据订单切换产能和节拍,满足雷达小批量、多品种、变节拍生产需求。车间设置缓存库和线边库,整个生产物流形成“缓存库–线边库–工位”三级物料配送模式,通过自动导引车(AGV)、电动叉车进行物料周转与配送。车间内物流路线主要以直线物流为主,简洁高效。
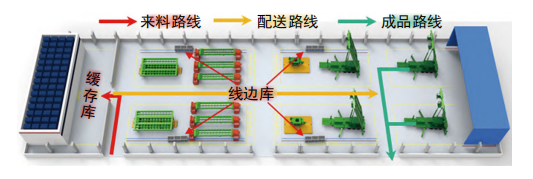
图 8 数字化工厂生产布局
5.2 生产管理系统建设
信息系统为产品和业务服务,因此在进行数字化工厂建设过程中,首先需要结合企业目标实现全流程透明,并在此基础上打造一体化、数字化平台。结合前期的调研及分析工作,面向雷达装备多品种、小批量、变节拍的柔性生产需求,开展数字化工厂建设,消除生产制造端的业务痛点与难点。
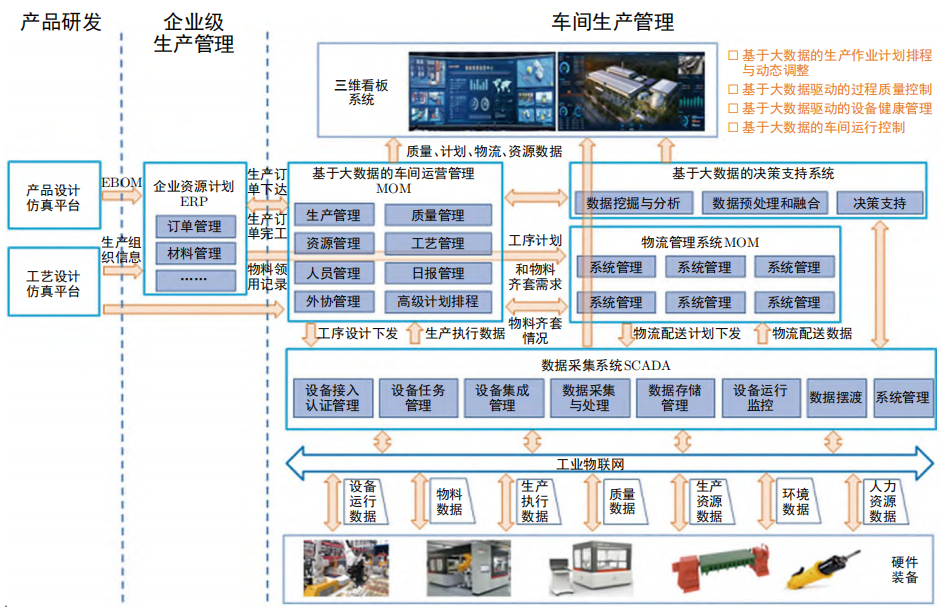
图 9 数字化工厂生产管理系统架构
围绕数字化工厂生产管理系统架构(图 9),以生产过程的端到端数据贯通为目标,搭建企业资源规划(ERP)系统、车间运营管理系统(MOM)、仓储管理系统(WMS)、监控与数据采集(SCADA)系统、车间可视化展示系统(WVS)的车间信息化管理架构,实现基于大数据的工厂运营管理。
其中车间运营管理系统实现生产计划、生产资源等的管控;物流管理系统实现车间物料管理和配送管理;数据采集系统作为车间管理系统与生产设备数据传递的中枢,实现生产计划等数据的下达和生产过程数据采集;可视化系统实现生产过程数据的综合展示。目前已实现了跨车间的制造工序协同,关键生产设备数据实现实时采集,初步具备了可视化辅助决策能力。通过对生产数据的深度挖掘,实现了生产需求与生成资源的高效匹配。
6.结束语
本文通过雷达电子装备制造业中的一个具体项目,系统研究了该项目实现数字化的实施路径,从业务流程梳理、问题调研、基于 KPI 的改善权重分析和数字化实施工作计划建立,形成了数字化实现的基本方法论。最后,通过数字化工厂建设, 论证了该方法论具有可实施性。该项目已经完成了既定的目标,初步具备可视化辅助决策能力,实现了企业运营管理的巨大提升。该方法可以推广至其他数字化项目,为其他制造企业的数字化实现提供借鉴。
评论