人工智能与数字双胞胎:如何通过虚拟模型实现智能工厂管理?
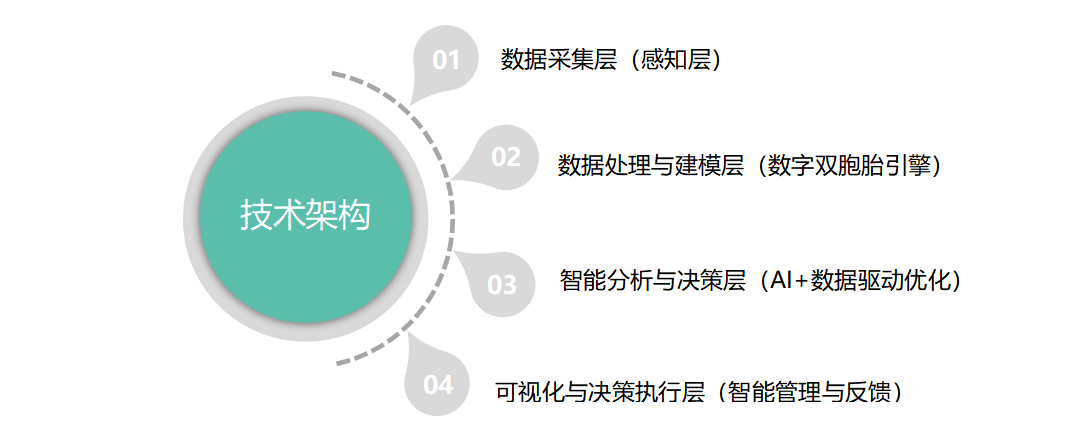
引言:智能制造的未来趋势
全球制造业正迎来一场深刻的变革,智能制造已成为企业提升竞争力的关键。然而,许多企业仍面临生产效率低下、设备维护成本高、供应链不透明等难题。如何在保证质量的同时提升生产效率?如何降低设备故障率,减少停机损失?如何优化资源配置,实现柔性生产?这些都是智能制造亟需解决的问题。
在这一背景下,人工智能(AI)与数字双胞胎(Digital Twin) 正成为推动智能工厂发展的核心技术。人工智能能够基于大数据和机器学习,实现精准预测和智能优化,而数字双胞胎则通过构建虚拟模型,实现对物理工厂的实时监控与仿真。当两者结合,工厂不仅可以实时感知生产状态,还能通过 AI 分析进行预测性维护、智能调度和能耗优化,从而打造高度自动化、柔性化的智能制造体系。
那么,人工智能与数字双胞胎如何具体应用于智能工厂?企业该如何落地这项技术,实现降本增效?本文将探讨二者的结合如何赋能智能工厂,并通过实际案例展示其在生产优化、设备管理、质量控制等方面的应用价值。
一、数字双胞胎与人工智能的核心概念
1、什么是数字双胞胎?
数字双胞胎(Digital Twin) 是物理世界在数字空间中的精准映射。它通过实时数据采集、仿真建模和智能分析,构建出与真实物理对象高度一致的虚拟模型,实现对设备、生产线乃至整个工厂的全面监控和优化。
一个完整的数字双胞胎系统通常包括:
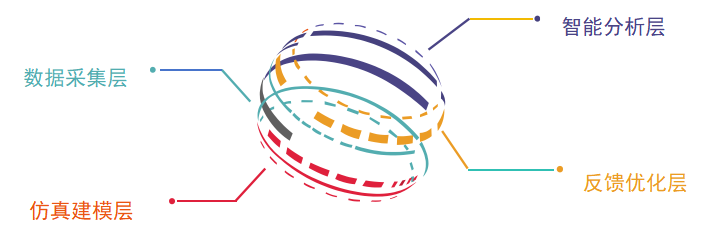
数据采集层:通过传感器、物联网(IoT)、工业互联网等技术,实时采集设备运行、环境状态、生产工艺等数据。
仿真建模层:利用 3D 建模、物理引擎、工业大数据等技术,创建与真实系统匹配的虚拟工厂或设备模型。
智能分析层:结合人工智能和大数据分析,对生产过程进行优化、预测性维护、质量控制等。
反馈优化层:基于虚拟模型的分析结果,优化物理系统的运行策略,实现闭环管理。
2、人工智能在智能工厂中的作用
人工智能(AI)在智能制造中扮演着“大脑”的角色,主要体现在以下几个方面:
智能优化生产流程:AI 算法分析历史生产数据,自动优化生产计划和资源配置,提高产能。
预测性维护:机器学习模型基于设备历史运行数据,预测可能的故障,提前采取维护措施,减少非计划停机时间。
质量检测与缺陷预测:计算机视觉结合 AI,可以自动检测生产中的缺陷,并通过深度学习预测质量问题的发生概率。
能耗优化:AI 分析设备能耗数据,调整运行参数,降低生产过程中的能源消耗。
3、AI 赋能数字双胞胎,提升智能工厂管理
虽然数字双胞胎本身能模拟物理系统,但传统的仿真依赖固定规则,无法动态适应复杂的制造环境。而 AI 的加入,使数字双胞胎具备了自学习、自优化和预测能力,从而真正实现智能制造:
更精准的仿真:AI 结合传感器数据,使数字双胞胎的模型不断优化,更接近真实生产环境。
更高效的预测分析:AI 可以实时分析双胞胎模型的数据,发现潜在问题并提供最优解决方案。
自动化决策支持:基于 AI 分析,工厂管理者可以获得智能决策建议,甚至让系统自动调整生产策略。
AI+数字双胞胎的结合,正在推动智能工厂从“被动响应”向“主动优化”转变,让制造企业真正实现降本增效、柔性生产和智能决策。
二、智能工厂中的关键应用场景
人工智能(AI)与数字双胞胎(Digital Twin)的结合,让智能工厂的管理从传统的“被动应对”升级为“主动优化”。在实际应用中,这项技术主要体现在以下几个关键场景:
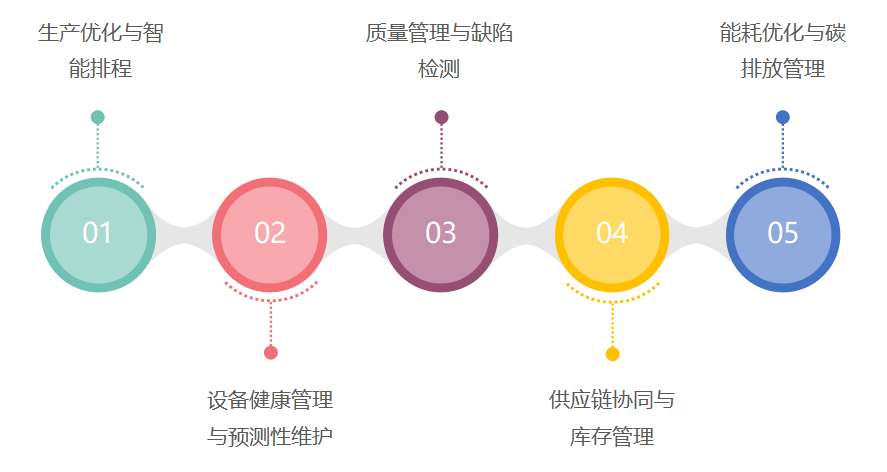
1、生产优化与智能排程
痛点: 传统生产计划往往依赖人工经验,排产不合理会导致资源浪费、交付延期,甚至影响生产效率。
AI+数字双胞胎如何优化?
AI 结合历史生产数据、订单需求、库存情况,动态调整生产计划,提高设备利用率。
数字双胞胎模拟不同排产方案,评估最优生产策略,减少切换成本和瓶颈环节。
通过实时数据监控,自动调整生产节奏,确保交付准时性。
应用效果: 生产效率提升 10%-30%,订单交付率提高 20%以上。
2、设备健康管理与预测性维护
痛点: 设备故障无法提前预测,维修往往发生在设备停机后,导致生产损失和维护成本增加。
AI+数字双胞胎如何优化?
通过 IoT 传感器实时监测设备温度、振动、电流等状态数据,AI 分析异常趋势,预测潜在故障。
在数字双胞胎中模拟设备运行状态,提前发现磨损、过载等问题,提前安排维修。
AI 自动生成最优维护计划,减少不必要的检修,提高设备寿命。
应用效果:设备停机时间减少 40%-50%,维护成本降低 20%以上。
3、质量管理与缺陷检测
痛点: 传统质量检测依赖人工或抽检方式,容易出现漏检,且问题发生后才处理,造成损失。
AI+数字双胞胎如何优化?
结合计算机视觉和 AI 算法,实现生产线上的实时自动检测,提高检测精度。
在数字双胞胎中模拟产品制造过程,预测可能出现的质量问题,并优化工艺参数。
通过 AI 分析质量数据,找到缺陷根因,优化工艺流程,减少次品率。
应用效果: 质量缺陷率降低 30%-50%,人工检测成本减少 50%。
4、供应链协同与库存管理
痛点: 供应链信息不透明,缺乏精准预测,容易造成库存积压或断供风险。
AI+数字双胞胎如何优化?
AI 预测市场需求,优化原材料采购计划,避免库存积压。
通过数字双胞胎仿真供应链流程,提高库存周转率,减少资金占用。
AI 自动协调供应商交付,动态调整库存策略,确保生产连续性。
应用效果: 供应链成本降低 15%-25%,库存周转率提高 20%-30%。
5、能耗优化与碳排放管理
痛点: 传统工厂的能耗管理方式粗放,难以精准优化能源使用,增加了生产成本和碳排放压力。
AI+数字双胞胎如何优化?
AI 分析各生产设备的能耗模式,找出能耗异常点,优化能源分配策略。
通过数字双胞胎模拟不同能耗方案,实现最优能源管理,减少浪费。
结合碳排放数据,优化生产工艺,降低碳足迹,满足环保要求。
应用效果:能源消耗减少 10%-20%,碳排放降低 15%以上。
总结
人工智能与数字双胞胎的结合,正在深刻改变智能工厂的管理方式。从生产优化、设备维护、质量管理、供应链协同到能耗管理,AI+数字双胞胎为制造企业提供了更精准、高效的运营模式,帮助企业实现真正的降本增效、智能决策和可持续发展。
三、技术架构与实现方式
人工智能(AI)与数字双胞胎(Digital Twin)的结合,为智能工厂提供了全方位的智能化管理方案。要实现这一目标,需要构建一个完整的技术架构,涵盖数据采集、建模仿真、智能分析、可视化交互等多个层面。
1、技术架构概览
智能工厂的 AI+数字双胞胎架构可以分为四个核心层次:
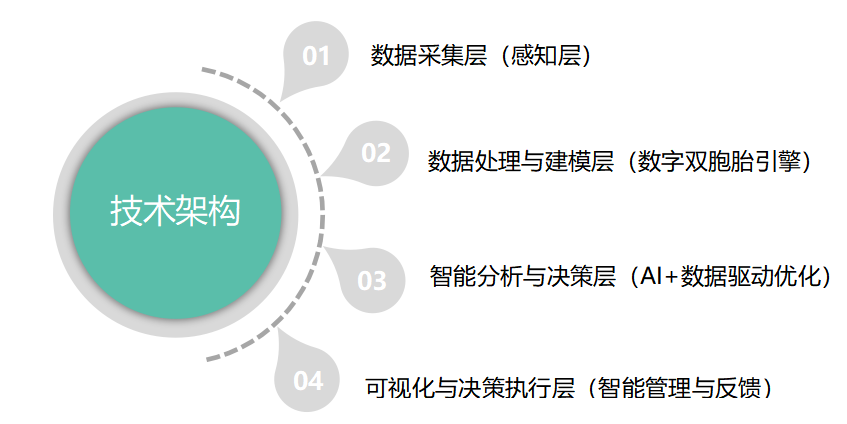
(1)数据采集层(感知层)
核心功能:通过各种传感设备采集工厂的实时数据,为数字双胞胎提供基础信息。
主要技术:
工业物联网(IIoT):通过传感器、RFID、PLC(可编程逻辑控制器)、SCADA(数据采集与监控系统)等采集设备运行、环境状态、生产进度等数据。
5G 与边缘计算:提升数据传输速度,减少数据延迟,提高本地数据处理能力。
应用示例:
在生产线上部署振动传感器和温度传感器,实时监测设备运行状态,AI 分析后预测故障趋势。
(2)数据处理与建模层(数字双胞胎引擎)
核心功能: 利用 AI+仿真建模,构建数字双胞胎模型,实现对物理工厂的动态模拟。
主要技术:
三维建模与仿真(3D Simulation):使用 CAD、BIM、Unity 等技术创建虚拟工厂。
物理引擎:结合 AI,模拟生产设备的运行状态,如温度变化、磨损程度等。
大数据处理与 AI 分析:利用机器学习、深度学习算法分析工厂数据,实现智能预测。
应用示例:
构建完整的工厂数字双胞胎,通过仿真测试不同生产方案,找到最佳排产策略。
(3)智能分析与决策层(AI+数据驱动优化)
核心功能: 通过 AI 算法分析数字双胞胎数据,提供智能决策支持。
主要技术:
机器学习(ML)/深度学习(DL):用于预测设备故障、优化生产计划。
计算机视觉(CV):用于产品质量检测、异常情况识别。
强化学习(RL):用于优化工厂调度,提高生产效率。
应用示例:
AI 分析历史设备故障数据,训练预测性维护模型,提前预警设备可能的损坏。
(4)可视化与决策执行层(智能管理与反馈)
核心功能: 通过可视化界面和自动化控制系统,将分析结果转化为实际决策并执行。
主要技术:
3D 可视化(Digital Twin Dashboard):实时展示工厂运行情况,提高管理透明度。
自动控制(Industrial Automation):结合 PLC、MES、ERP 系统,实现生产自动调整。
智能反馈闭环:AI 自动优化参数,实时调整生产策略,实现智能决策。
应用示例:
在数字双胞胎平台上查看工厂实时运行情况,AI 自动调整机器转速以降低能耗。
2、智能工厂的闭环优化流程
整个系统通过以下闭环流程实现智能优化:
数据采集:通过传感器、IoT 设备收集设备状态、生产数据、环境信息。
数据处理:将采集的数据传输至云端或边缘计算节点,进行清洗、存储、分析。
模型仿真:利用 AI 与仿真技术,构建虚拟工厂,模拟不同优化方案。
智能分析:AI 对数据进行分析,预测故障、优化生产计划、降低能耗。
决策与执行:将优化建议传输至 MES、ERP 等系统,实现智能控制。
持续优化:AI 自学习,基于历史数据不断优化预测与决策模型。
3、关键技术落地挑战与优化方向
虽然 AI+数字双胞胎为智能工厂提供了强大的能力,但在实际落地过程中仍面临挑战:
(1)挑战
数据孤岛问题:不同生产设备、系统的数据格式不统一,难以整合。
计算量大,实时性要求高
AI 模型适配性问题:不同工厂的设备和工艺不同,AI 模型泛化能力受限。
企业转型成本高
(2)优化方向
采用工业互联网协议(OPC UA),统一数据标准,推动跨系统集成。
结合边缘计算+云计算架构,在本地进行快速计算,减少云端延迟。
采用自学习 AI 模型,结合迁移学习,提高适配能力。
采用低代码+模块化架构,降低企业数字化门槛,推动智能工厂建设。
4、未来发展趋势
随着 5G、边缘计算、量子计算、低代码开发等技术的发展,AI+数字双胞胎在智能工厂中的应用将进一步升级:
更精准的 AI 建模:AI+物理仿真相结合,提升数字双胞胎的精准度。
全自动化智能工厂:数字双胞胎+AI+机器人,实现无人化生产。
工业元宇宙(Industrial Metaverse):结合 AR/VR,实现沉浸式工厂管理与远程维护。
总结
AI+数字双胞胎的技术架构,从数据采集、建模仿真、智能分析到决策反馈,构建了一套完整的智能工厂管理体系。通过不断优化技术架构,未来的智能工厂将更加自动化、柔性化、低成本化,为制造业带来全新的生产模式和竞争力。
四、案例分析:AI+数字双胞胎如何助力智能工厂?
AI 与数字双胞胎的结合,已经在多个行业的智能工厂中落地应用,帮助企业优化生产、降低成本、提升效率。以下是几个典型的应用案例,展示 AI+数字双胞胎如何赋能智能制造。
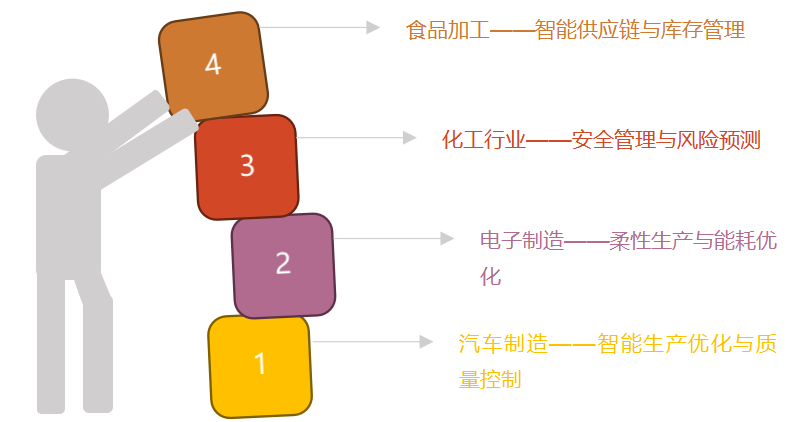
案例 1:汽车制造——智能生产优化与质量控制
背景问题
某大型汽车制造企业在生产过程中面临生产调度复杂、质量检测效率低、设备维护成本高等挑战。
解决方案
生产优化:
采用 AI+数字双胞胎,模拟不同排产方案,动态调整生产线,减少瓶颈环节,提高生产效率。
结合 AI 预测市场需求,优化库存管理,减少物料积压和缺货风险。
智能质量检测:
计算机视觉+深度学习,对焊接、喷涂等关键工序进行自动检测,提高检测精度和速度。
设备预测性维护:
通过数字双胞胎实时监测生产设备状态,AI 分析传感器数据,预测可能的故障,提前安排维护,避免生产停机。
应用成效
✅生产效率提升 20%,交付周期缩短。
✅质量缺陷率降低 35%,产品一致性提高。
✅设备停机时间减少 40%,维护成本降低。
案例 2:电子制造——柔性生产与能耗优化
背景问题
某电子制造企业面临产品种类多、订单需求变化快、生产过程能耗高的问题,难以实现柔性制造和低碳生产。
解决方案
数字双胞胎+AI,实现柔性制造:
构建完整的数字双胞胎工厂,模拟不同生产方案,根据订单需求动态调整生产线配置,提高柔性制造能力。
AI 能耗优化:
通过 AI 分析设备能耗数据,优化能源使用策略,减少不必要的电力浪费。
在数字双胞胎中模拟不同工艺参数,找到最优能耗控制方案,实现降本增效。
应用成效
✅订单响应速度提升 30%,生产切换成本降低。
✅单位产品能耗降低 15%,生产成本减少。
✅碳排放减少 18%,符合绿色制造标准。
案例 3:化工行业——安全管理与风险预测
背景问题
某化工企业由于生产过程涉及高温、高压、危险化学品,存在较大的安全隐患,传统管理方式难以及时发现风险。
解决方案
AI+数字双胞胎安全监测:
在化工厂部署传感器,实时监测温度、压力、气体浓度等关键参数。
AI 分析数据,结合数字双胞胎仿真,预测可能的安全风险,提前采取应对措施。
智能应急响应:
AI+仿真技术模拟突发事故的可能影响,优化应急预案,提高事故响应能力。
应用成效
✅安全事故发生率降低 50%,生产安全性大幅提高。
✅紧急响应时间缩短 30%,降低损失风险。
✅生产合规性提高,满足严格的环保和安全监管要求。
案例 4:食品加工——智能供应链与库存管理
背景问题
某食品加工企业由于原材料保质期短,供应链复杂,容易出现库存积压或缺货问题,影响生产效率。
解决方案
AI+数字双胞胎智能供应链管理:
通过 AI 分析市场需求,预测销售趋势,优化原材料采购计划,减少浪费。
在数字双胞胎系统中模拟不同供应链策略,优化库存周转,提高供应链效率。
应用成效
✅库存积压减少 25%,资金占用降低。
✅原材料浪费减少 30%,降低成本。
✅订单履约率提高 20%,客户满意度提升。
总结
以上案例表明,AI+数字双胞胎在智能制造、质量管理、设备维护、安全监测、能耗优化、供应链管理等方面都能发挥巨大作用。通过精准的数据分析和仿真优化,企业可以实现降本增效、智能决策、可持续发展,真正迈向智能工厂时代。
五、未来展望与挑战
AI 与数字双胞胎的融合正在推动智能工厂向更高效、更智能、更可持续的方向发展。然而,在广泛应用的过程中,仍然面临诸多挑战。未来的发展趋势和解决方案将决定这一技术的落地深度和普及速度。
1、未来展望:智能工厂的演进方向
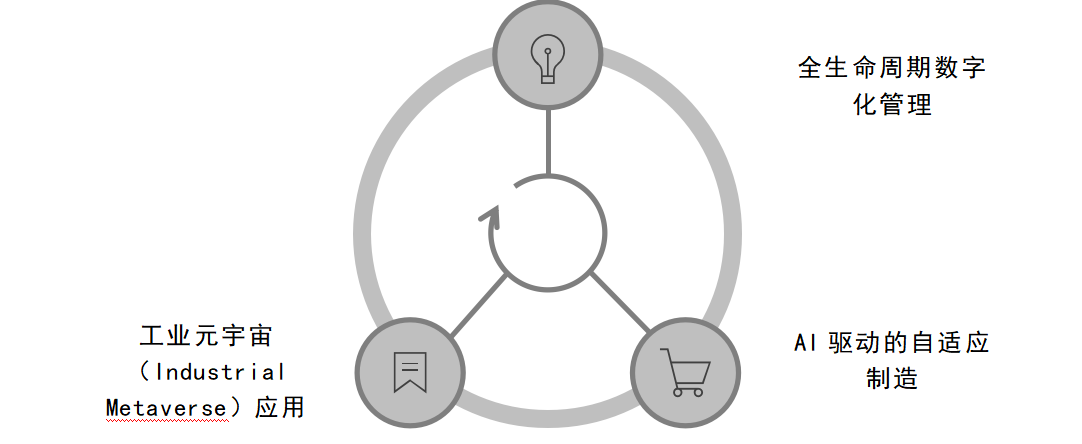
(1)全生命周期数字化管理
未来的智能工厂将实现从设计、生产到运维的全生命周期数字化管理。
✅产品设计:在产品研发阶段,AI+数字双胞胎可以用于仿真测试,优化设计方案,减少试错成本。
✅生产运营:生产过程中,工厂可以通过智能排产、实时监控和预测性维护,实现更高效的管理。
✅设备运维:工厂的所有设备将拥有数字孪生体,能够进行远程诊断和智能维修。
案例:某航空制造企业已使用数字双胞胎优化发动机设计,使燃油效率提高 10%,降低维护成本 30%。
(2)AI 驱动的自适应制造
未来,AI 将进一步提升智能工厂的自学习、自优化能力,推动制造模式的个性化和柔性化。
✅自适应生产:AI 能够实时调整工艺参数,动态适应不同订单需求,减少换线成本。
✅实时优化:AI 结合数字双胞胎,实时仿真并调整生产策略,提高生产效率。
✅自主决策:基于强化学习的 AI 可自主优化供应链、库存和能耗,实现更精准的生产管理。
案例:特斯拉的“无固定生产线”模式,结合 AI 和数字双胞胎,实现自动调整生产配置,提高柔性制造能力。
(3)工业元宇宙(Industrial Metaverse)应用
未来,AR/VR、5G 和 AI 的结合将推动工业元宇宙的发展,使远程操控、虚拟培训和沉浸式管理成为现实。
✅远程工厂监控:管理人员可在虚拟空间内查看全球各地工厂的实时运行情况。
✅沉浸式培训:员工可以在数字双胞胎模拟的环境中学习操作,提高技能水平。
✅远程故障诊断:专家可在元宇宙工厂中分析设备问题,并提供远程指导。
案例:西门子与 NVIDIA 合作,打造工业元宇宙,使制造企业能够在虚拟环境中设计、测试和优化生产线。
2、面临的挑战与应对策略
挑战 1:
数据孤岛问题:生产设备、业务系统数据格式不统一,难以整合
应对策略 1:
采用工业互联网协议(OPC UA),统一数据标准,实现互联互通
挑战 2:
AI 模型的泛化能力不足:工厂的工艺、设备不同,AI 训练的模型难以适用于所有场景
应对策略 2:
采用自学习 AI+迁移学习,让 AI 能根据新环境不断优化
挑战 3:
计算资源消耗大:AI+数字双胞胎计算量大,实时仿真需要高性能算力
应对策略 3:
结合 云计算+边缘计算,提高计算效率,减少延迟
挑战 4:
企业实施成本高:数字双胞胎系统部署复杂,前期投资较大
应对策略 4:
采用低代码+模块化架构,降低企业的技术门槛和实施成本
挑战 5:
数据安全与隐私风险:工厂的生产数据涉及商业机密,容易被黑客攻击
应对策略 5:
加强区块链+边缘计算,确保数据安全和访问权限控制
3、结论:迈向真正的智能制造
未来,AI+数字双胞胎将成为智能工厂的核心技术,推动制造业向更高效、更智能、更可持续的方向发展。虽然挑战仍然存在,但随着技术的不断成熟和标准化,智能工厂将逐步普及,实现真正意义上的无人化生产、自主优化和智能决策。企业若能提前布局,将在全球竞争中占据先机,引领未来制造业的发展。
总结
AI 与数字双胞胎的结合,正在深刻变革智能制造,为企业提供前所未有的优化生产、降低成本和提升决策能力的机会。从数据采集、仿真建模、智能分析到自动化执行,这一技术体系正在帮助工厂迈向更高效、更智能、更可持续的未来。
通过案例分析可以看出,无论是汽车制造、电子加工,还是化工行业、食品生产,AI+数字双胞胎都能有效提升生产效率、减少能耗、优化供应链,并提升安全性。而随着技术的不断演进,未来的智能工厂将具备更强的自适应能力,实现全生命周期的智能管理和自主优化。
当然,挑战依然存在,企业在落地过程中需要解决数据孤岛、AI 模型泛化、计算资源消耗、实施成本高等问题。然而,随着工业互联网、低代码开发、云计算+边缘计算、区块链安全技术的发展,这些问题将逐步得到解决。
未来,智能工厂不仅仅是一个“生产车间”,更将成为一个能够自主学习、优化、预测和决策的智能生态系统。企业若能抢先布局,利用 AI+数字双胞胎提升竞争力,就能在未来制造业的竞争中占据领先地位,实现真正的数字化转型和智能化升级。
版权声明: 本文为 InfoQ 作者【天津汇柏科技有限公司】的原创文章。
原文链接:【http://xie.infoq.cn/article/2dd394c5f63525e1de85f7ba1】。
本文遵守【CC-BY 4.0】协议,转载请保留原文出处及本版权声明。
评论