专家观点∣数字化场景应用助力铁合金企业增产提效
数字化场景是各类主体围绕一项或多项特定需要,运用数字技术推动服务要素整合、业务系统集成、运营模式创新,提供实时、定向、互动、闭环数字化应用体验的重要载体。
某铁合金冶炼民营企业,是行业细分领域的龙头企业,近年来,经营类信息系统建设走在行业领先水平,已经完成了多轮迭代,经营提效能力得到了很好的释放;近两年,企业完成了产业出海以及国内规模扩张,企业老板审时度势,拟发挥自身规模化优势,提出在保障安全的前提下提高产量,创造更好的效益。
结合数字化场景数据智能、控制高效、技术融合、沉浸体验等特点和用户提高产量的最终诉求以及用户实际生产工艺特点,抽丝剥茧,层层递进,从更少的停机、更稳定的工艺、更透明的生产以及更高效的控制梳理形成整体数字化转型 15 大场景,解决产量提高以及效率提升问题。
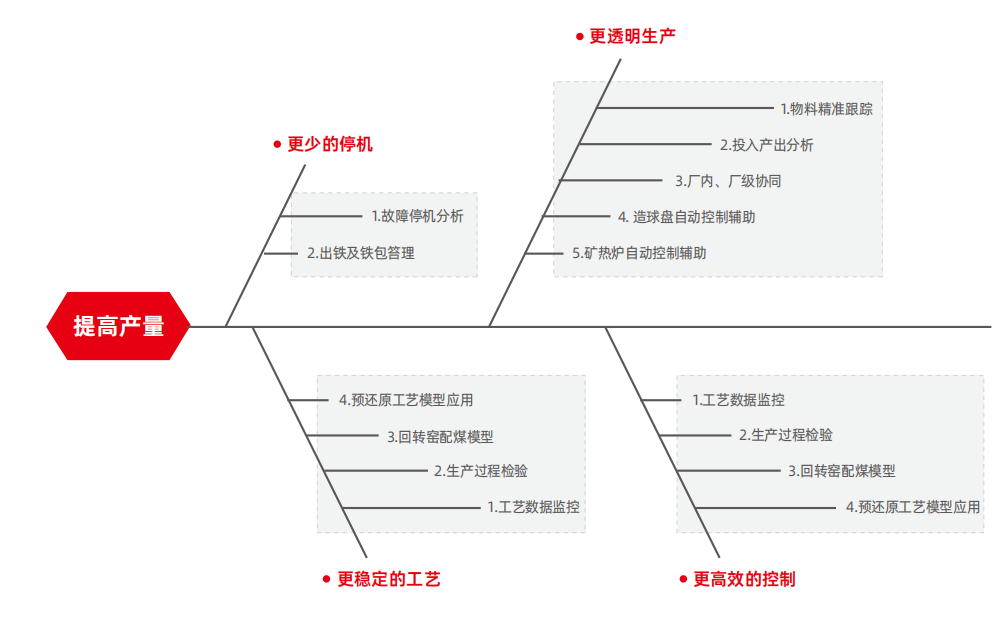
移动应用、沉浸体验
提高用户控制效率
铁合金行业工艺控制较为复杂,生产节奏快、供料复杂,原料品种多,来料成分配比不同,工艺控制要求不同,完全需要实时掌握来料变化情况,特别是成分、水分、挥发分等检验数据,根据来料变化适时调整工艺。在原料库及皮带、筒仓等上料过程建立基于移动 APP 的原料精准跟踪数字化应用场景,将原料卸货、地仓上料、皮带拉料、筒仓存储、配料,装置(球磨机、链蓖机、回转窑、矿热炉)上料等过程进行数字建模,基于“先进先出”原理实现在线可视化展示来料、变料、配比数据,如下示意图所示,帮助工艺控制人员一目了然掌握来料情况,便于工艺快捷调整,稳定生产,提高效率。
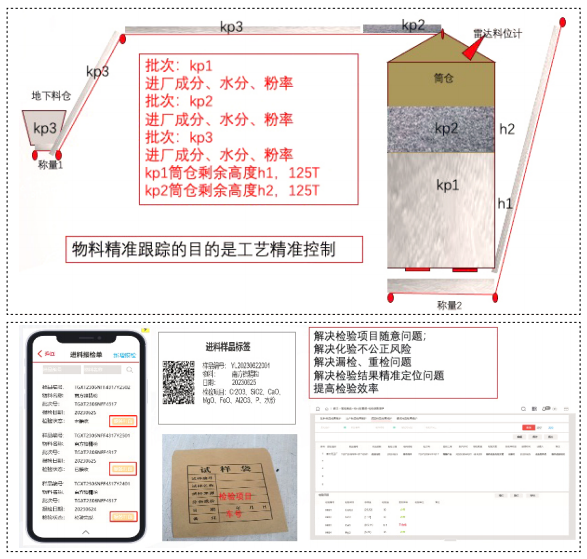
同时工艺生产过程中需要取样及化验,现场取样工基于生产过程检验数字化场景,如下图所示,通过 APP 实现精准取样、样条(加密供应商信息)自动打印及快速委托,在增强用户应用感受,规避风险的同时提高过程检验效率,有效支撑工艺精准控制。
智能装备、技术融合
提高现场管控效率
矿热炉主要是通过电极加电升温,电极桶内需要维持一定高度的电极糊,传统电极糊测量方式是人工抛绳测量,受测量频率及测量环境影响,无法实时测量掌握糊柱高度。电极操作管理数字化场景中对人工抛绳测量方式进行了优化,引入智能化雷达测距仪,对每个电极桶内糊面进行实时测量,并对测量数据进行实时监控,有效支持岗位工人的精准加糊,为矿热炉稳定生产提供了有效支撑。
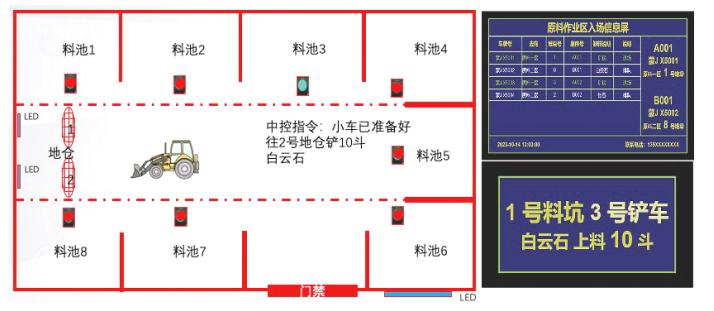
一定规模的铁合金企业原料库众多,很多原料外型相似,特别是不同品味矿粉,肉眼无法直接分辨,原料精准跟踪数字化场景对料堆进行精细化管理,如下图所示,对各个料池进行精准设定,车辆到来时,结合算法(均匀堆放、安全库存、取样最少等规则)自动分配车辆去向,并通过库房门口 LED 车辆导引,提高车辆卸货效率。同时原料地下料仓上料计划通过料池指示灯与料仓 LED 屏配合引导,支持铲车司机精准上料,提高原料现场管控效率。
知识汇集、控制高效
提高整体控制水平
铁合金行业工艺自动化控制水平较低,很多企业工艺控制基本靠人工经验,不同的人控制水平参差不齐,同时人员流失量大,人员离开,经验流失。标准操作管理数字化场景从两个方面收集工艺控制经验(一方面作业指导书中可量化的控制要求,另一方面工艺人员“口口相传”的控制经验),形成专家知识库,通过工艺数据监控数字化场景及 IOT 物联魔方能力对工艺运行情况进行实时监控及预警,如下图所示,并对预警情况进行诊断和建议,有效提升整体工艺控制水平。
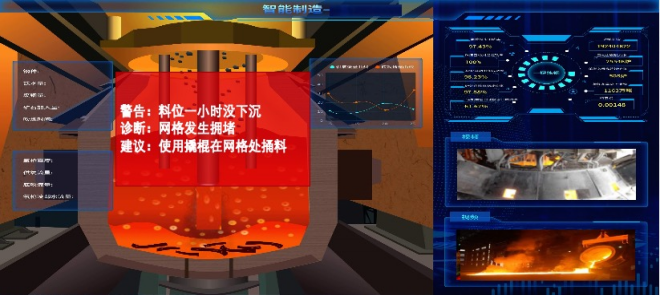
矿热炉冶炼追求工艺稳定性,工艺越稳定,产量越大。传统的工艺控制只关注了工艺控制数据是否超过控制上下限,觉察不到工艺的细微变化,SPC 数理统计分析工具拥有 8 大判异规则,能准确识别工艺微小异常变化;能对工艺过程稳定性进行指标评价,工艺数据监控数字化场景集成 SPC 数理统计分析判异报警及控制图分析,有效指导用户提高工艺控制稳定性,确保产线稳产、高产。
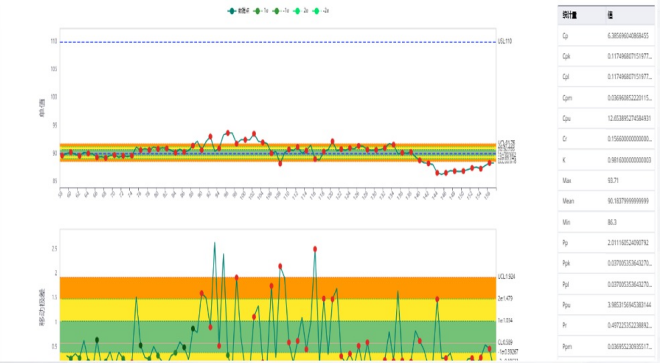
算法模型、数据智能
提高工艺控制精度
大数据时代工艺控制指导不仅可以通过冶金机理模型应用也可以通过数理统计模型应用,如下图所示,铁合金企业回转窑焙烧主要通过煤气或者煤粉燃烧供热,回转窑配煤模型应用数字化场景,主要解决的回转窑煤气使用与煤粉使用平衡问题,通过收集回转窑正常焙烧情况下链蓖机机速、料厚,煤气流量、高温段温度,煤粉使用量以及助燃机风量等数据,基于回归算法模型,建立 F(w 煤粉 ,V 风量) y=f(T 料厚,V 机速,V 煤气, T 球,T0 )函数关系,通过一定周期内链蓖机机速、料厚,煤气流量、高温段温度等数据预测煤粉使用量及助燃机风量,有效指导回转窑燃烧控制,提高回转窑工艺控制精度,降低能耗。
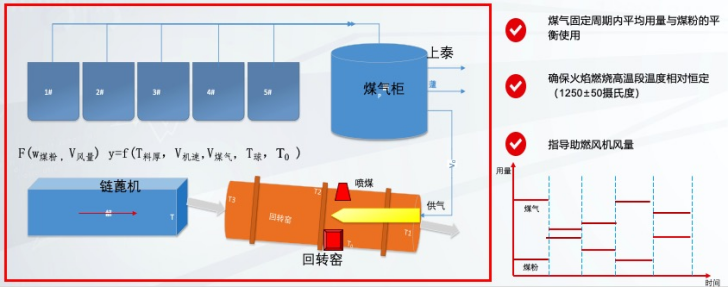
评论