制造企业实施 MES 系统受到的影响因素有哪些?
实施 MES 系统会遇到哪些影响因素?或者说企业实施 MES 系统的交付率为什么低?
我觉得关键点在于:在当前 MES 产品化程度普遍不高的大环境下,对项目及管理软件本身认知过于简单,且缺失有经验行业人才,是当前大部分 MES 系统影响交付的主要原因。
回首过往,国内 MES 行业基本存在以下几点情况:
1、智能制造建设需求迫切、企业 MES 系统需求旺盛;
2、制造企业对 MES 的投资金额有所增加,并且有向高投资额区间偏移的趋势;
3、MES 系统的产品化程度仍较低,制造企业更多以自主研发或合作开发的方式实施 MES 系统;
4、MES 项目实施成功率不高,达到预期效果的项目只有一半。
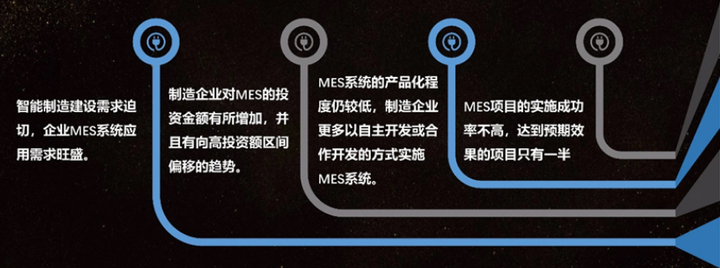
导致这些情况的原因在于“智能制造”是近些年才热起来的,与当初的互联网热一样,这股热潮吸引了大批从其他领域转入的从业者。与成熟的 ERP 市场不一样,MES 领域目前还是处于一片蓝海,寡头未现,犹如作春秋战国时期,各地诸侯自成一方。在给你们企业做 MES 项目的项目经理可能之前是做 ERP 项目转行来的,产品经理可能之前是做电商系统转行来的,开发很有可能是从小程序转行过来的。对于 IT 行业经验丰富的大神们,虽然不能快速的摸清其中的门道,但依葫芦画瓢抄一抄前辈们的作业还是很在行的。
基于此,下面本文将讨论 MES(制造执行系统)领域的现状,并与成熟的 ERP 领域进行比较。从管理、设计、实施和人才四个维度进行分析。这些观点是作为一个从业者对 MES 行业的初步理解。欢迎指出和讨论任何不正确或不准确的地方。
企业实施 MES 系统存在的影响因素有:
1、低估了“管理”在整个项目中的比重
制造企业面临管理问题,尤其是与生产相关的问题。管理需要有效的信息传递和互通,包括工单、处理单、报告、会议等。信息化系统可以提高管理效率、降低沟通成本。然而,在管理水平较低的企业,即使使用管理系统也难以改善管理问题。管理系统只是辅助工具,需要有人能够有效使用。
MES 系统是生产管理系统的核心,涉及人员、设备、物料、仓库、物流、工艺、计划和质量等方面。信息化管理需要重新构建整个生产管理流程和体系。这需要管理层仔细分析每个系统设计的利弊得失,而不是由外部公司随意决定。
管理软件将管理逻辑数字化,但一个字段或逻辑的偏差可能对生产造成巨大影响。在分配项目资源时,可以借鉴软件巨头 SAP 或国内织信低代码的咨询顾问模式。管理咨询能力是关键,SAP、织信等平台都建立了自己的人才梯队和认证体系。在解决管理问题时,可以进行用户访谈、业务重构、需求汇总和系统设计,让企业用户参与并明确项目需求和目标。
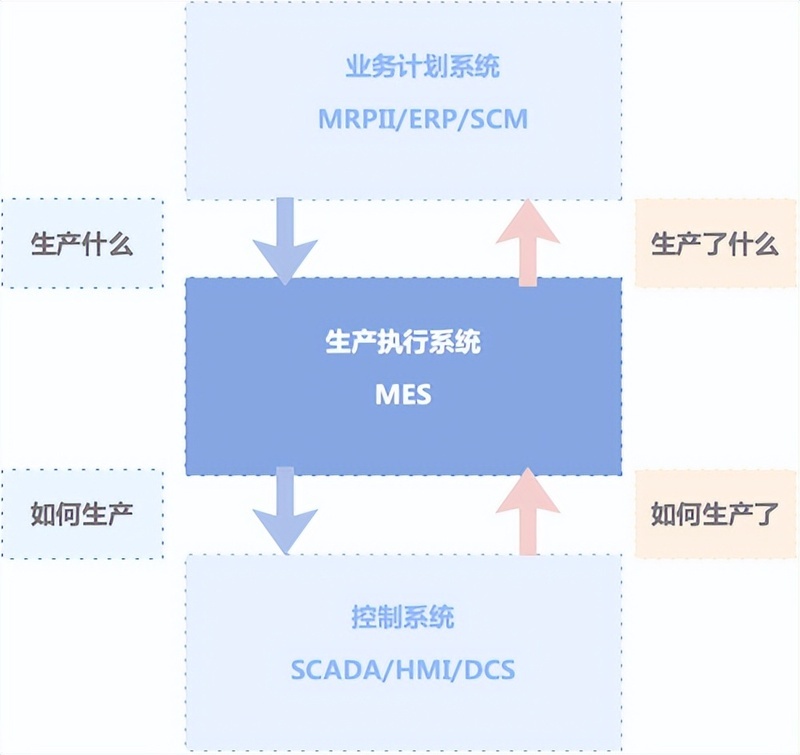
2、低估了整个系统“设计”复杂度
MES 系统的标准产品化存在困难,主要是因为管理体系本身的复杂性。德国工业软件之所以强大,是因为他们将各种管理业务形态纳入一个管理体系,并要求它们相互融合不冲突。这需要从最基础的理论研究开始,将所有业务拆分到最小颗粒并进行分类。这部分工作超出了日常程序员的职能范围,需要业务专家和系统设计师承担。
MES 系统承载了制造企业对生产管理的理解和业务逻辑,而不同的生产产品、模式和工艺会导致不同的管理需求。这使得实现 MES 系统的产品化变得复杂,需要深入了解制造工艺知识和管理业务逻辑。
国外的 MES 产品更像是开发平台,需要由本地化的实施团队进行业务设计和管理构建。相比之下,对于管理软件来说,开发能力门槛并不高,但真正掌握系统需要深入理解其中的管理思想和业务逻辑。要设计好制造行业的 MES 产品,需要成为当前行业的半个业务专家,并深入了解每个数据背后的意义。
MES 系统的设计复杂程度与 ERP 系统相当甚至更高,涉及到工艺管理、任务管理、排产、质量管理、设备管理、仓储管理、物料配送、供应链等方面。要做好 MES 系统设计,需要花费数年的时间和精力来学习制造及管理知识,并进行优化改良。这是一个漫长的过程,需要不断的尝试、试错、反思和总结,与客户共同寻找最优解决方案。

3、低估了整个系统“实施”困难度
MES 系统实施难度大,原因主要体现在管理和设备互联方面。管理方面的困难在于覆盖范围广,涉及到大量现场生产人员,而设备互联方面需要解决不同品牌、型号设备的数据采集问题。
对于管理方面的实施困难,例如一个 200 人规模的制造企业,大部分人员都与现场生产相关,仅有少部分是办公室管理人员。以前实施 ERP 系统都需要很长时间,而且只涵盖了一部分办公室人员。对于 MES 系统来说,它需要覆盖工厂所有生产相关人员,人数比 ERP 系统的实施范围更广,因此实施难度更大。
设备互联方面,企业使用的设备种类和品牌多样,甚至不同时代的设备可能同时工作。这导致在设备数据采集和联网方面出现了许多实施上的问题。有些设备需要改造才能进行数据采集,而有些设备的数据受到保密处理,需要购买专门的接口才能获取准确的信号。这些情况增加了实施的工作量和难度。
针对这两个实施难题,可以采取以下解决思路。在管理方面,通过管理咨询和系统设计降低实施的难度。可以在管理咨询阶段将数据初始化等工作分发给关键用户和员工完成,培养他们处理问题的能力。在系统设计阶段,让客户参与全过程,让他们了解软件的设计并提出需求,避免后期修改带来的问题。这样可以提高工作效率,降低实施工作量,并增加客户满意度。
在设备互联方面,可以将专业的事情交给专业的人处理。对于一些冷门设备的数据采集问题,可以引入专业公司解决,而将 MES 系统的核心放在管理部分。这样可以避免长时间的技术攻坚过程,控制项目周期和实施成本。最后,通过统一的数据汇总实现底层设备的连接。这几个方面也正是企业级低代码平台所擅长的地方。
以上是针对 MES 系统实施难度的解决思路,供参考。
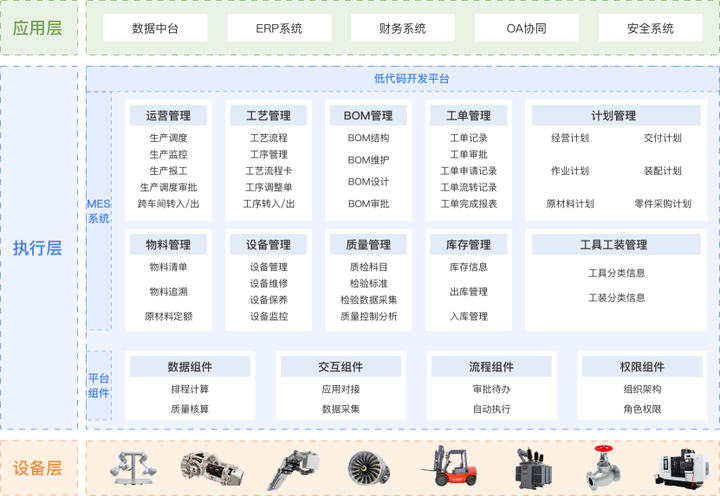
4、行业“人才”梯队还未成规模
当前 MES 领域产品化程度较低,主要以定制化开发为主。有些人错误地认为开发是万能的,只要需求清晰开发就能快速完成系统软件。这种模式在简单需求下可能有效,但在复杂业务场景下容易遇到瓶颈。全能型人才并不常见,因为每个人的精力和专业能力都有限。
在构建 MES 等定制化管理系统时,业务专家是核心角色,需要懂管理和系统设计,作为需求方和开发方之间的连接人。他们理解高层目标和管理需求,将传统管理业务结构化,协助企业进行信息化管理流程和体系改造。他们与管理团队合作逐层剖析和细化变革目标,并针对不同角色的使用场景进行定制化系统设计。最好由一个人负责整个项目,避免协调问题和结果偏差。
目前 MES 行业人才梯队尚未完全培养出来,初入行业的公司和从业者面临挑战。虽然无法解决行业人才紧缺问题,但可以努力提高团队水平和能力,培养更多业务专家,加强他们的管理咨询和系统设计能力,更好地服务于定制化 MES 项目。
这是对当前 MES 领域产品化程度、开发模式和业务专家角色的简化描述。
结语:
总的来说,近年来制造企业实施 MES 系统受到的影响因素主要有如下几点:
行业不成熟,许多公司无经验就涌入该领域,用标准定义来忽悠客户,无法满足真正需求。
销售和售前人员只关心签下项目,不负责实施,导致项目交付困难。
MES 产品化和标准化难度高,需要逐个行业突破,缺乏好的标准和产品。
项目中缺少经验丰富的行业人才,导致项目失败。
一些公司缺乏专业性和专注度,市场需要真正专业且有价值的公司和从业者。
MES 行业改善是长期过程,需要共同努力,留下专业且有价值的人们,市场会自然淘汰不合格的公司和从业者。
所以,加油吧~
评论